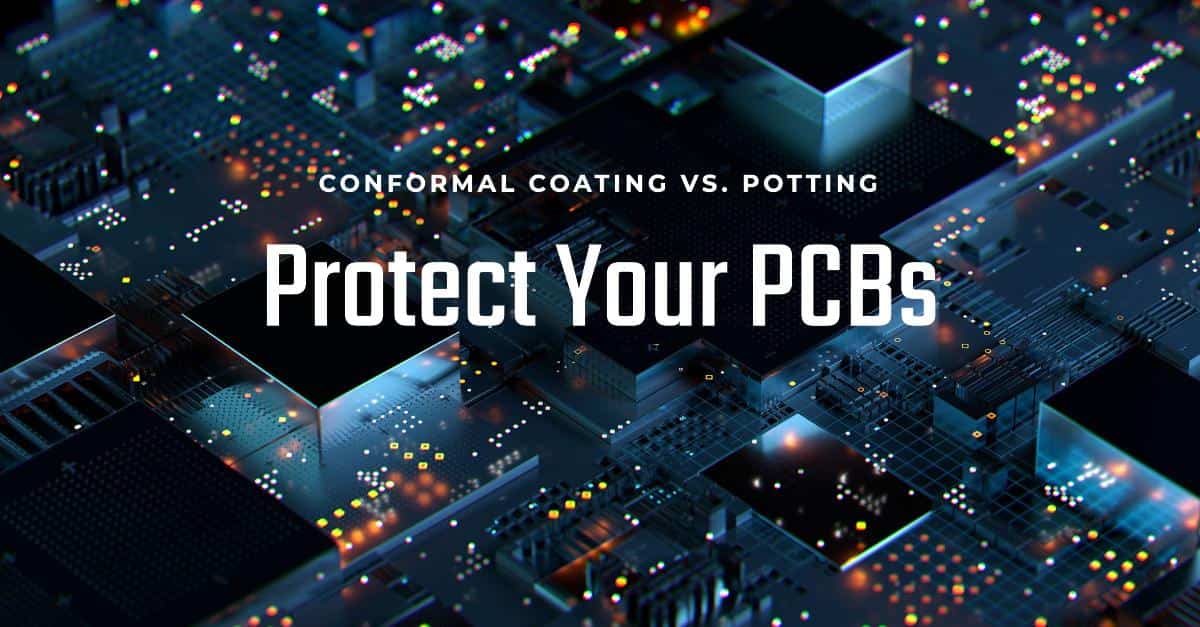
Introduction
Eminent PCB or Printed Circuit Board manufacturers like Rush PCB Inc. often protect their boards with either a layer of conformal coating or by potting them. The choice depends on the purpose of the PCB and the amount of protection necessary. Although potting offers a substantially strong shielding barrier, it also introduces many operational disadvantages offsetting its functional benefits. On the other hand, conformal coatings offer reliable barrier protection that helps to circumvent the issues inherent in potting. In this article, we will compare the two and assist in making an informed decision about which of them to use.
Why Electronic PCBs Need Protection
Exposure to harsh environments can often harm electronic components including PCBs, damaging them or wearing them out. Conformal coatings and potting offer protection for electronic components from a range of environmental factors that can be potentially damaging. These could include salt, chemicals, moisture, dust, mechanical abrasives, and vagaries of temperature. With a reliable conformal coating or potting, electronics can withstand corrosion and other types of damage.
What is a Conformal Coating?
Conformal coating is a thin layer of protection conforming to the structural and environmental characteristics of the PCB. The operator applies it by hand brushing, spraying, or dip coating. While providing adequate protection from many environmental factors, conformal coatings improve the operational integrity and increase the dielectric resistance. It helps to protect the PCB and components from dirt, dust, heat, fungus, humidity, and other corrosive atmospheres. Conformal coatings offer several advantages:
- Long life expectancy
- Relatively low expense
- Flexible design
- Reduced need for complex enclosures
- Minimal contribution to weight increases
- Excellent protection against particulate matter and corrosion
- Reduce warranty claims
- Improve product reliability
- Allows reworking, inspection, and repair
There are several types of conformal coating types depending on the needs of the application:
Coating Type / Parameters |
PARYLENE | SILICONE | EPOXY | URETHANE | ACRYLIC |
Water Resistance | Excellent | Fair | Good | Good | Poor |
Curing Necessary? | No | Yes | Yes | Yes | Yes |
Application Stress | None | Low | High | High | High |
Abrasion Resistance | Good | Fair | Excellent | Excellent | Good |
Thermal Cycling | Excellent | Excellent | Good | Good | Fair |
Adhesion | Excellent | Excellent | Excellent | Good | Good |
Dielectric Strength | Excellent | Fair | Excellent | Excellent | Good |
Chemical Resistance | Excellent | Good | Excellent | Excellent | Good |
Coating Quality | Excellent | Good | Good | Good | Good |
Advantages and Disadvantages of Each Type of Coating
Each type of conformal coating has its advantages and disadvantages as below:
PARYLENE CONFORMAL COATING | |
ADVANTAGES | DISADVANTAGES |
Excellent protection from water | Method of application — Vapor deposition only |
Extreme resistance to chemical substances | Specialized equipment necessary |
Outstanding dielectric properties | Batch processing process |
No pinholes and uniform coverage | |
Parylene conformal coatings are thermoplastic film and ultra-thin. They provide the best-in-class protection against moisture, extreme temperatures, and solvents. The industry considers them as the gold standard for reliability among all other conformal coatings. Typical application is where field repair, failure, and or expensive warranty claims cannot be a practical option. |
EPOXY CONFORMAL COATING | |
ADVANTAGES | DISADVANTAGES |
Excellent resistance to abrasion | Possibility of cracks or shrinkage may cause stress on components |
Very good resistance to chemical substances | Complex mix ratio and difficulty maintaining viscosity |
Good protection against moisture | Requires curing |
Epoxy conformal coatings are hard and rigid and are available as two-part mixtures. They provide excellent mechanical wear resistance, good moisture, and chemical protection in harsh environments. Not recommended for applications subjected to extremes of temperature and excessive vibration, as these can cause shrinkage and cracking failures. |
URETHANE CONFORMAL COATING | |
ADVANTAGES | DISADVANTAGES |
Very good dielectric properties | Requires long cure times (30 days) |
Excellent resistance to chemicals | Additional equipment necessary to expedite curing |
Excellent resistance to abrasion | Non-uniform coating, typically thick |
Urethane conformal coatings are very well suited for extreme chemical and rugged conditions. Low material costs and flexible application methods make urethane coatings affordable. However, it requires a long curing time, or additional equipment to reduce curing times. This can increase the total coating cost. |
SILICONE CONFORMAL COATING | |
ADVANTAGES | DISADVANTAGES |
Excellent for temperature cycling and extreme temperatures | Tacky material that other processes can contaminate |
Good resistance to humidity | Low resistance to abrasion |
Coating is resilient and flexible | Curing necessary |
Good dampening for vibrations | |
Silicone conformal coating offers excellent protection against temperature cycling and extreme temperatures. They are good for outdoor storage, offering good resistance to humidity, chemicals, and salt-water spray. Its rubbery, tacky nature offers poor protection against abrasion, but good resilience against vibrational stress. |
ACRYLIC CONFORMAL COATING | |
ADVANTAGES | DISADVANTAGES |
Easy to apply | Chemical resistance is poor |
Provides a basic level of protection | Potential for high VOC |
Easy to remove for field repair | Coating viscosity is difficult to maintain |
Acrylic conformal coatings are good for basic entry-level protection. They offer low-cost protection against many types of contaminants but do not offer the best-in-class for any. They are easy to remove, making them practical and economical for rework and field repair. Acrylic coatings offer weak protection against solvents. |
What is Potting?
Unlike the thin, single-layer conformal coating, potting is a two-step process. Here, the operator first inserts the PCB to be protected into a case or shell. They pour a liquid potting compound into the case, over and around the PCB, allowing the liquid to encase it completely. As the liquid dries, the filled pot becomes part of the final product. Potting protects sensitive components from water and moisture damage. Colored potting compounds can act as a visual and physical barrier preventing tampering and IP theft. Potting offers the ideal choice for:
- Vibration damping
- Good heat dissipation
- Good impact resistance
- Good abrasion resistance
- Good impact resistance
- Good chemical resistance
- Protection against arcing
- Preventing tampering
- Protecting IP theft
- Easy to use in high-volume applications
However, potting has some disadvantages:
- Reworking potted assemblies is extremely difficult
- Increase in assembly weight due to encasement and potting
- Compound shrinkage can damage the PCB
- The use of underfills for enhancing shock-robustness may cause failure during thermal cycling.
Popular Potting Compounds
Potting Compounds | Properties |
Urethane | High flexibility, easy to work with for common electronic substrates. Urethane has excellent abrasion resistance and ensures that internal components remain safe. |
Epoxy | Most common potting compounds provide excellent adhesion. Offers excellent flexibility and tensile strength. |
Silicone | Very popular for applications requiring extensive temperature range. Although expensive, they barely exert any stress/pressure on the PCB components. |
Selection Criteria for Potting Compounds
Designers must pay attention to certain aspects when choosing their potting material:
Hardness
Hard potting compounds are best suited for applications requiring weather resistance and IP protection. Silicone potting compounds offer extreme hardness.
Viscosity
Although the industry preference for potting is based on low-viscosity compounds, some applications require high-viscosity potting materials.
Color
Dark-colored potting materials significantly hinder visibility, making it difficult to identify or locate individual components. Although this is preferable for preventing tampering or protecting against IP theft, it can be an impediment for lighting applications using LEDs, where a light-colored potting material would be preferable.
Thermal Conductivity
As the potting material completely encompasses the PCB and its components, the thermal conductivity of the potting compound is of significant importance. Almost all PCBs emit heat during use, which means a potting material with high thermal conductivity is essential.
Comparing Conformal Coatings and Potting
CONFORMAL COATINGS | POTTING |
Method of application: hand brushing, dip coating, or spraying | Method of application: requires a case or shell to house the PCB and the potting compound completely fills the case, surrounding the PCB entirely.
However, potting may protect individual components as well. |
Applied in a thin layer conforming to the structural and environmental characteristics of the PCB. | |
Provides improved operational integrity, improves dielectric resistance, and offers significant protection against environmental factors like fungus, humidity, dust, dirt, heat, and corrosive elements. | Provides improved operational integrity, improves dielectric resistance, and offers significant protection against environmental factors like fungus, humidity, dust, dirt, heat, and corrosive elements. |
Supports reworking, inspection, and repair | Does not support reworking, inspection, and repair. Provides protection from electric arcs in high-voltage electronics. |
Preserves boards with sensitive components and applies minimal physical stress to the substrate. | Very effective in damping vibrations, impact resistance, preventing tampering, and preventing IP theft. |
Takes up very little space within the device enclosure and is comparatively lightweight. | Fast and efficient application process suitable for assembly lines. |
What Protects PCBs Better — Conformal Coating or Potting?
Whether conformal coating will be better than potting or vice versa for PCBs will depend on the application that requires protection. The engineer must consider the intended use of the device, including the conditions it must endure, both during manufacture and in the field. The most common considerations would be:
- Conditions the PCB will be exposed to in the manufacturing process
- Possible elements the PCB will be exposed to in its working environment
- Design of the enclosure housing the PCB
- Other protections from environmental factors included in the device
in most cases, the selection depends on the purpose for which the PCB is intended. While both conformal coating and potting offer improved durability, the PCB may not require that much protection. Depending on the application, potting may significantly increase the weight, hindering other product requirements.
Potting is a popular choice for heavy-duty applications and the industry often uses it for high-voltage electrical devices. Engineers prefer potting for environments in extreme conditions such as mines, factories, and power plants. Potting is beneficial for high-throughput production environments that demand improved durability and resistance to abrasion and scratches.
On the other hand, conformal coating is best suited for sensitive devices and components where the form and size are critical concerns. Being lightweight and thin, conformal coatings are most suited for handheld electronics like smartphones.
Conclusion
Before making a final decision on whether to go for conformal coating or potting, Rush PCB Inc. suggests discussing with the PCB manufacturer. Both conformal coating and potting are complex processes offering unique variables determining turnaround time, effectiveness, and cost. Consulting the PCB manufacturer can help to select the optimum protection for the project, its timeline, and budget.