Use of Printed Circuit Boards (PCBs) in ultra-high vacuum environments and during wave or hand soldering can release gases trapped within them. This is a concern when using PCBs in outer space, medical facilities, and laboratories, as vapors escaping from the PCB can condense on the rest of the equipment. Even when the vapor is relatively harmless and familiar, such as water, in outer space it can interfere with the operation of lenses and optical equipment by contaminating them. Rush PCB, an eminent PCB manufacturer uses proper techniques for manufacturing PCBs with the lowest risk of outgassing.
During solder reflow or even during manual soldering, moisture trapped within boards can outgas and vaporize because of the heat, ultimately venting through the nearest through-hole, thereby creating voids in the solder mask.
Manufacturers make PCBs of a variety of porous composites. During the manufacturing process, these permeable materials often trap vapors such as air, inside them. Application of heat during soldering or operation in high vacuum can force the vapors out from a PCB, and this is known as outgassing.
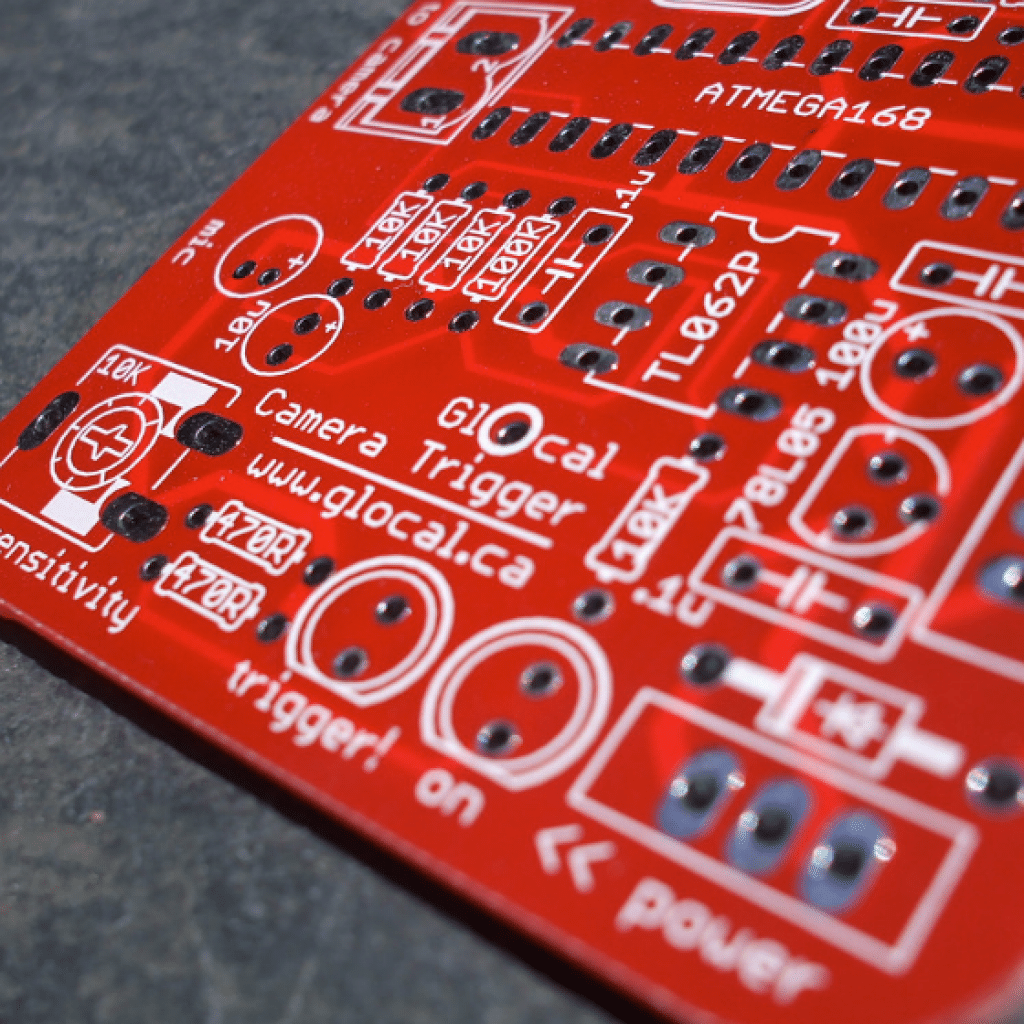
Reasons for Outgassing
There are two main reasons for the occurrence of outgassing. The first is faulty manufacturing processes, and the other is use of incorrect material.
Faulty Manufacturing Processes: The quality of a PCB largely depends on the manufacturing processes. If the pre-heating process is inadequate or the electroless copper plating is too thin, outgassing can happen during soldering. Moreover, inadequate removal of moisture during the production process can allow PCB materials to retain moisture during manufacturing, leading to outgassing during high-vacuum applications or during soldering.
Use of Incorrect Material: The board’s lifecycle, including its manufacturing and application, define the materials the designer and the manufacturer must consider for building the PCB. For instance, PCBs with a plating of tin, silver, or gold may contain organics or salts that release gas when heated. PCBs for use in high-vacuum applications are typically made of materials with a lower instance of outgassing to reduce the risk.
Outgassing a Major Problem
Outgassing often produces condensate vapors that interfere with optical instruments, contaminating measurements. For instance, in space probes meant for measuring cometary atmosphere, outgassing could obliterate the cometary signature.
NASA recognizes outgassing as a major problem and offers tips for testing materials for outgassing. However, even after following these guidelines, PCBs will experience some level of outgassing. Therefore, it is necessary to focus not only on limiting outgassing from PCB components, but also on mitigating its effects.
Reducing Outgassing
Rush PCB bakes their PCBs to remove moisture. Water absorbed by boards can vaporize and release gases during solder reflow causing different types of defects. In space applications, the same vapor or moisture can outgas in the void of space. Baking the PCB in vacuum ensures residual moisture reduces to a minimum.
Rush PCB selects materials with proper thermal resistance when making their PCBs. This reduces the risk of outgassing. For instance, they use materials designed for very low outgassing, such as RT/Duroid series from Rogers Corporation and flexible circuit material such as Kapton, which offers low outgassing characteristics.
Apart from choosing the right materials made for vacuum application, Rush PCB also uses a vacuum pre-bake process as it helps to remove as much moisture as possible from the boards.
Mitigating Outgassing
Even the use of the best materials and fabrication processes may not always remove outgassing altogether. Therefore, engineers have some mitigation strategies in place for keeping the PCB working in the event of outgassing. They use heating elements and vent vapor away from instruments to reduce its effects.
As outgassing is a problem of lens or other optical instrument contamination, one way to prevent released moisture from PCBs from reaching sensitive surfaces is to direct it away from them by designing a path for the gases to follow and exit to areas where they can do little harm.
When the above is not possible, engineers use heating elements to burn off the vapors and prevent them from depositing on sensitive apparatus.
Although it is difficult to design PCBs for application in ultrahigh vacuum, Rush PCB uses some of the best professional PCB design software and professional techniques to manufacture PCBs. The excellent array of tools help build PCBs that can operate not only on the ground, but also above it.
Evaluating Materials for Outgassing
NASA has developed exacting procedures for evaluating materials for outgassing. For instance, their test procedure SP-R-0022A is meant for testing composite materials such as circuit-board laminates.
Procedures such as the ASTM E595-07, from ASTM International, is useful in gauging key material parameters such as TML or total mass loss, and CVCM or Collected Volatile Condensable Material for evaluating the changes in mass that different materials undergo in vacuum environments such as during outgassing. The ASTM process evaluates the change of mass in test specimens under vacuum at a temperature of 125°C over a period of 24 hours. NASA accepts materials only if its TML is lower than 1% and the CVCM is lower than 0.1%.
ASTM and NASA do not insist on the vacuum levels during the tests to be similar to that of deep space, which can be 10-14 Torr or 10-12 Pa. For these tests, it is adequate if the vacuum is of the order of 5×10-5 Torr or 7×10-3 Pa. However, the choice of 125°C is at least 30°C above typical operating temperature, and it creates accelerated lifetime conditions.
Once the 24-hour period under high temperature and high vacuum ends, the specimen has to be weighed at 23°C and 50% RH, according to the ASTM standard. This minimizes the effects of water vapor on the accuracy of the measurement. During the 24-hour heating period, samples are placed within a glass vial. After the 24-hour period, the samples must be weighed within a 2-minute period after opening the vial, so that loss of absorption of water vapor is minimized as the sample is exposed to an uncontrolled environment. Sometimes, as additional test is also performed for WVR or Water Vapor Recovered. Test labs perform outgassing tests on materials both before and after curing them.
High-Quality Materials
Rush PCB uses high-quality materials and well-controlled manufacturing processes that lead to low levels of outgassing. They use circuit-board materials made by eminent manufacturers such as Rogers Corporation. These materials tested according to NASA test procedure SP-R-0022A, show measurements for CVCM, TML, and WVR well-suited for applications in space. These materials are composites of RT/Duroid, based on PTFE or Polytetrafluoroethylene along with inorganic filler materials, such as ceramic and glass fillers and temperature-stable hydrocarbon composites of the TMM series.
Conclusion
While not a concern for all circuit designers, the material characteristic of outgassing affects electronics for spacecraft and satellites, and hence not a matter to be considered lightly. Typically, Rush PCB selects materials with the lowest CVCM, TML, and WVR values available for circuit boards.