From being purely mechanical assemblies, automotive vehicles have progressed to include electronic parts. A top brand automotive vehicle today contains about 150 control units consisting mostly of sensors and processors. According to a study, more than 60% of the electronics exists within the dynamical system, the body, and the chassis of the automotive vehicle, while most of it concerns digital signals and power electronics. The study estimates the share of electronics in automotive vehicles will soon cross 70%.
According to Rush PCB, automotive systems with electronics require Printed Circuit Boards (PCBs). While the global requirement of PCBs for the automotive industry was US$4.6B in 2014, the latest estimates put this figure over US$7B by 2020. This increase of electronics in automotive performance has resulted in improvements in:
Environmental Aspects: There have been tremendous improvements in fuel saving and exhaust reduction.
Security Aspects: There is reduction in traffic accidents.
Convenience and Comfort Aspects: There is increased use of air-conditioners, computers, communication, and entertainment equipment inside automotive vehicles, making them more convenient and user-friendly.
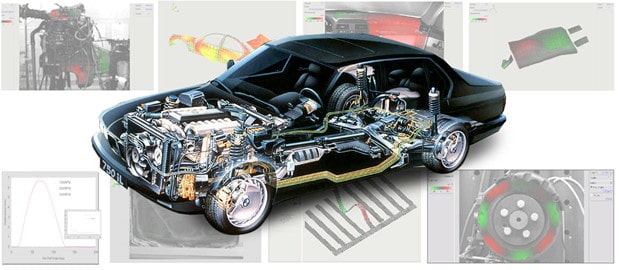
Requirements of PCBs in Automotive Vehicles
It is necessary that PCB manufacturers catering to the automotive industry conform to international standards such as ISO 9001. Rush PCB complies with the ISO 9001:2015 Quality Management System and adheres to the strictest standards of manufacturing and assembly.
In 1994, the automotive industry followed the QS9000 quality control system. However, in the early 2000s, the industry was following a new quality control system ISO/TS16949, based on the ISO 9001 standards.
PCB Reliability: The industry measures reliability of automotive components in two aspects—lifespan and environmental. Lifespan reliability requires components to perform normally within the entire lifespan of the vehicle. Environmental reliability requires all components to continue functioning without changes even when there is a change in the environment.
Presently, the industry-expected lifespan of an average automotive vehicle is about 10 to 12 years, and the electronic systems and PCB must perform normally within this period, without failure.
While operating, automotive vehicles must withstand environmental changes such as from extremely hot summers to freezing cold winters, from frost to rain to sunlight, and internal temperature changes as a result of regular operations. Apart from temperature excursions, automotive electronic systems including PCBs must withstand current surges, electronic interference, mechanical vibrations, and humidity.
PCB Categories: Modern automobiles contain electronic equipment at different positions and performing different functions, which require a variety of PCBs. Based on the use of substrate materials, automotive PCBs follow a general classification of two main categories—organic resin-based and inorganic ceramic-based PCBs. The automobile industry widely uses organic resin-based PCBs in different positions for different functions. The industry relies on inorganic ceramic-based PCBs where high temperature resistance is necessary, as these have excellent dimensional stability, making them suitable for applications in motor systems operating at high temperatures.
Read About: IPC STANDARDS FOR PCBS
In general, the industry also uses rigid and rigid-flex PCBs for gauges indicating vehicular speed, mileage, and in air-conditioning equipment. Audio and video entertainment equipment within vehicles also use such double- and multi-layered flex PCBs. In-vehicle security control equipment, wireless positioning equipment, and communications equipment regularly use flex, multi-layered, and HDI PCBs. Automotive power transmission and motor control systems require use of special boards such as metal-based PCBs.
High-Frequency Substrates: Automobiles with predictive braking and collision resistance safety systems require transmitting microwave high-frequency signals. These require PCBs with substrates using low dielectric loss materials such as PTFE. These require special drilling and feeding speeds during drilling.
Thick Copper PCBs: Advanced electric power transmission systems and increasing electronic functions in automobiles requires PCBs capable of supplying large currents and handling higher heat dissipation. PCBs with thick copper traces meet these requirements of high current. While fabricating double-layer PCBs with thick copper is relatively easy, fabricating multi-layered PCBs with thick copper in the inner layers is more difficult.
PCBs with Embedded Components: For decreasing product size, it is necessary to increase the assembly density. One of the ways of doing this is by using PCBs with embedded components. Mobile phones and automotive electronic equipment use this technology intensively. Manufacturers use several methods for fabricating PCBs with embedded components, most popular among them being the excavation method, lamination method, ceramic method, and module method. The advantage of using PCBs with embedded components is their relatively higher reliability, which suits the automotive requirements of resistance to vibration, humidity, and heat.
HDI Technology: Most entertainment and communication equipment in automotive electronics require HDI PCBs with multiple layers. This technology involves micro-vias with laser drilling, plating, and lamination positioning for automotive PCB manufacturing.
Read About: DIFFERENT STACKUPS FOR HDI PCBS
Testing Reliability of Automotive PCBs
As automobiles belong to high-reliability product category, and there are concerns with public security, PCBs meant for automotive use must pass special reliability tests, such as:
TCT or Thermal Cycling Tests: Based on their position within the automobile, PCBs acquire one of five grades, with the TCT temperature range as:
Grade | PCB Position | Low Temperature | High Temperature |
A | Within the Cockpit | -40 °C | 85 °C |
B | Below the Base Shield | -40 °C | 125 °C |
C | Motor | -40 °C | 145 °C |
D | Driving Medium | -40 °C | 155 °C |
E | Inner Motor | -40 °C | 165 °C |
After the Thermal Cycling Test is over, automotive PCBs must work normally.
Thermal Shock Test: Automotive PCBs must work in environments with high temperature, especially the thick copper PCBs that produce their own heat as well. Therefore, automotive PCBs must have a higher heat resistance.
THB or Temperature-Humidity Bias Test: The THB test for automotive PCBs tests them in multiple environments, which includes humid environments such as during rainy days. Conditions for the THB test include temperature 85 C, relative humidity 85%, and DC voltage bias of 24V, 50V, 250V or 500V. THB test considers the Conductive Anodic Filament or CAF migration in PCBs, leading to reduction of insulation and short circuits.
Conclusion
According to Rush PCB, the constant upgrading of automotive electronics, and rapid changes in automotive technologies are pushing up the requirements and application of PCBs. Engineers and PCB manufacturers must consider and use new technology to meet the demands of the automotive industry. Rush PCB is fully capable of providing all types of automotive PCBs with high quality.