For Rush PCB, line efficiency is an extremely important business parameter. The faster a manufacturer turns out fully assembled PCBs that work as intended, the more its financial turn-over increases. If the PCB manufacturer operates continuously at low efficiency, before long they will be courting business failure, unless they can identify the root cause of the problem and remove it.
Also Read: CHOOSING THE PERFECT PCB ASSEMBLY PARTNER
For manufacturers of PCBs, line efficiency is the ratio of the number of hours a pick-n-place machine places parts on a PCB divided by the number of hours the staff attends to the SMT assembly line. Although various manufacturers measure line efficiency in different ways, one of them is by measuring capacity utilization, calculated by comparing production output to an average level of acceptable line efficiency and production.
While the production volumes for PCB manufacturers have increased to some extent, the number of individual product designs in the production schedule has increased significantly. Although some PCB manufacturers may still be producing large quantities of an individual product, a vast majority of them are now operating in a high-mix environment.
While changing over from low-mix to high-mix manufacturing, Rush PCB finds it necessary to optimize the throughput across multiple batches of different products, rather than favor the absolute throughput to optimize on a single item. Therefore, changeover times are now limiting the overall line utilization rather than the time it takes to start and end a specific build.
Calculating Line Efficiency
There can be two ways of calculating line efficiency of a PCB manufacturer, one by using production line efficiency, and the other using the SMT line efficiency. For most, the SMT line efficiency is a more appropriate metrics.
SMT line efficiency wins over production line efficiency, as the latter does not take duration into account. Production line efficiency considers only the time that staff spends on machines, rather than consider the actual use of labor. In fact, the assembly manager finds it difficult to control outside forces that affect productivity, whereas product volume the manufacturer must produce depends on market demand.
Also Read: MISTAKES TO AVOID FOR QUICKTURN PCBS
While calculating the SMT line efficiency, it is fairly easy to obtain the placement time and SMT time. Usually, the controller of the pick-n-place machine has a complete record of when the machine was placing the parts and it was not. Therefore, consulting the records identifies the placement time easily.
Rush PCB maintains a computerized record of staff time, which makes it easy to calculate the staffing hours. For proper calculations, breaks allowed to employees on company time are also included within the staffed hours. Rush PCB staggers the meetings, meal times, and other breaks so that the line is never left bereft during staff hours. This helps to maximize line efficiency.
This method of calculating the line efficiency results in clear and consistent results. Consistency is important as any changes made need to be studied for the effect it introduces in the line efficiency, and a consistent method provides a stable base from where to proceed further.
Improving Line Efficiency
While it is important to collect data for calculating line efficiency, analyzing the data is equally necessary. Rush PCB analyzes the collected data to determine the factors that can lead to improving a lagging line efficiency. Some parameters that the data analysis can lead to are:
- The optimum number of people on the line
- Functioning, age, and maintenance of the machines
- Line configuration and logistics issues
It is possible to improve the line efficiency by optimizing the above. However, for assessment of productivity, Rush PCB does not limit itself to SMT line efficiency measurements alone, and has alternate methods of measuring the effectiveness of the production line.
Alternate Methods of Optimizing Throughput
There are various lean manufacturing tools for making improvements in the reliability and productivity of the production processes. Two of the popular methods are Overall Equipment Effectiveness or OEE and Total Productive Maintenance or TPM. While TPM allows PCB manufacturers to maintain and improve the status of their production lines, OEE is a standardized performance metric for the operations based on the TPM concept and allows manufacturers a means to benchmark themselves against the performance of competitors in the same industry.
Overall Equipment Effectiveness
OEE, or the measure of overall equipment performance depends on six major causes of ineffective performance of a production line, such as machine availability, their performance, and the quality rate of their output. The six major factors are:
Major Causes of Ineffective Performance on a Production Line
Equipment Failure | Breakdown losses occurring due to sudden and unexpected equipment failure |
Process Failure | Failure occurring during process changing over, or adjustments for correct positioning. Also called Setup and Adjustment Losses. |
Idling & Minor Stops | Losses occurring during production interruption due to small parts blocking sensors or getting caught in chutes. |
Reduced Speeds | Losses occurring due to actual operating speed falling below designed speed |
Defects in Process | Losses occurring when products do not meet quality specifications and need reworking |
Reduced Yield | Yield losses occurring due to equipment requiring stabilizing time after startup, with first products not meeting specifications |
This is how the six major factors fit into the structure of OEE:
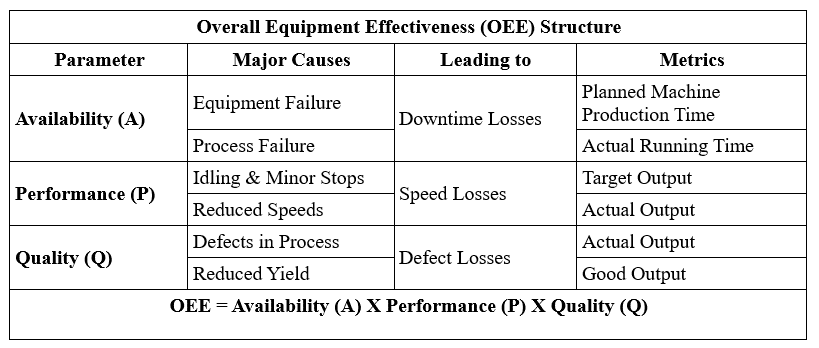
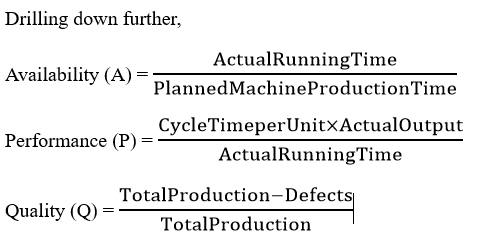
Quality (Q) =
Therefore, OEE offers a top view metric for indicating the gap between the initial and improved performance of the production unit. It concentrates on the productivity, performance, and quality of the machine. However, it does not address other resources of the production line, such as human efficiency, environmental factors, and the usage of materials.
Overall Resource Effectiveness
The above deficiency has led PCB manufacturers to use a modified approach, where they use the Overall Resource Effectiveness or ORE instead to address production process effectiveness. ORE addresses additional factors such as:
- Readiness (R)
- Changeover Efficiency (C)
- Availability of Manpower (AMP)
- Availability of Material (AM)
- Availability of Facility (AF)
Combining all the factors,

Difference Between OEE and ORE
The measurement of production process effectiveness in PCB production therefore depends on the parameters the manufacturer actually measures. This is because types of losses can vary between different production lines even within the same plant involved in high-mix manufacturing.
Factors beyond the control of the company may also cause production losses. These may include environmental changes, problems from third party logistics, internal factors such as non-qualified training, or other operation related causes.
The decision of choosing the metrics to measure depends on the PCB manufacturer and includes the specifications of the production lines. For instance, some PCBs may need specialized manual skills as one of the most important factors in its production process, in which case, ORE is the metric most suitable.
For fully automated production lines, OEE is more applicable for identifying and optimizing key performance indicators within the production line.
Conclusion
PCB manufacturers continually strive to improve their performance in the globally competitive business environment prevailing today. When making multiple batches of different high-mix products, they must continuously monitor and enhance the effectiveness of their production lines. Rush PCB uses different methods described above to keep a track on the effectiveness of their production lines.