Although manufacturers must deal with several variables when fabricating a Printed Circuit Board (PCB) including the solder mask, silk screen, copper width and weight, laminates form the foundation of the boards. Depending on the application, fabricators use different laminates, and this is a critical choice.
Manufacturers make laminates from thin layers of various materials such as fabric, fiberglass, or paper, using a resin to bond them together. Therefore, when fabricating the laminate, they can control the thickness by using more or a smaller number of layers. Thinner boards made with lower number of layers can be less rigid, and susceptible to flexing and broken traces.
By selecting the right laminate, the engineer determines the stability, losses, and optimum performance of the final PCB assembly. According to Rush PCB, the choice of materials depends on the environment in which the board will function, and three parameters mainly govern their choice:
- Coefficient of Thermal Expansion (CTE)
- Glass Transition Temperature (Tg)
- Dielectric Constant (Dk)
Coefficient of Thermal Expansion (CTE)
CTE of the laminate decides the amount of expansion or contraction a board will undergo with change in temperature. A laminate with a low CTE will not contract or expand much with large changes in temperature. When making laminates, the fabricator arranges the layers such that the CTE along the plane of the board is much lower than that perpendicular to it. This is because the latticework of the laminate constrains it from expanding along the plane.
An engineer must select a laminate with a low CTE to match with the low CTE of the copper layer on it. This is necessary as during thermal cycling, a laminate with a high CTE will tend to expand or contract more than the copper on it, leading to cracks forming on the traces and vias. If the board has only two or four layers, this may not be a serious concern. However, for thicker boards with small vias, when subject to extreme temperatures, higher CTE laminates can be a major concern.
Glass Transition Temperature (Tg)
During assembly, the PCB must go through a temperature rise high enough to melt the solder paste on it. For Lead-free solder paste, such high temperatures can soften the laminates to a more malleable form. Technically speaking, the PCB does not melt, but loses strict adherence to its original shape. Engineers call this the glass transition temperature (Tg), since the laminate starts to soften up beyond this temperature.
Lead-free solder paste melts at higher temperature as compared to regular Lead-based solder, and this melting point is closer to the Tg for most laminates. Therefore, Rush PCB recommends operators be careful not to let the PCB overheat or cross its Tg while soldering, as overheating may possibly warp the assembly. Operators adjust the thermal profile of their soldering machines to allow the PCB pass through the high temperature phase for a duration just enough to make the solder melt.
Dielectric Constant (Dk)
While the laminate acts as a mechanical platform for holding the components and copper traces, it also acts as an insulator preventing shorts between them. However, the laminate has electrical properties also that can affect the performance of high-frequency signals. Engineers call this the dielectric constant (Dk) of the laminate material, and it affects the complex interaction between the laminate and the high-frequency signals traveling through the traces.
Rush PCB recommends engineers use laminate with a predictable and stable Dk to allow them to accurately calculate the layout of the traces so that high-frequency signals do not degrade in operation. For instance, laminates made of PTFE have more predictable Dk compared to those made of FR4, which makes PTFE-based PCBs more suitable for handling high-frequencies.
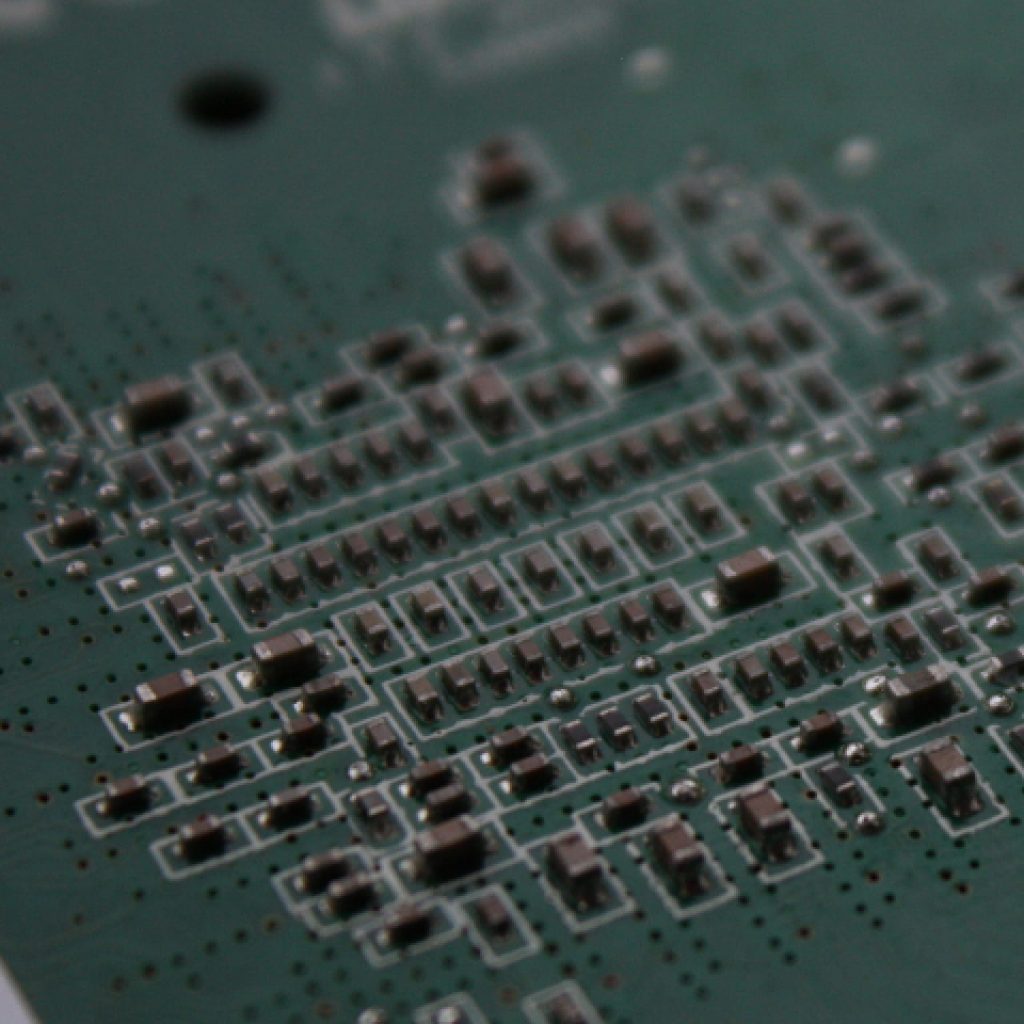
Thermal Conductivity
Although not a critical parameter while selecting laminates for a PCB, thermal conductivity of a board assumes importance when it has power devices mounted on it. As the heat must travel through the laminate until it reaches the copper acting as a heat sink, a higher thermal conductivity of the board helps in thermal management. With a higher thermal conductivity, the board can transport more heat away from the hot IC and spread it across a larger surface area, thereby resulting in better dissipation.
Read About: AVOIDING COMMON PCB FAILURE MODES
Cost
Cost is a very important variable in any design. Designers must balance performance and cost to get the most optimum results from a board. For instance, FR4 is the most inexpensive material for laminates, and it is easy to manufacture. However, its performance at high-frequencies is not acceptable, and designers must work with other more expensive laminates if their application demands the use of high frequencies and high-speed signals.
Common PCB Laminates
The electronic industry typically uses four types of laminates for PCB assemblies:
- FR-4
- High Tg Epoxy
- BT Epoxy
- Polyimide
While FR-4 is the most common laminate the industry uses for surface mount assembly, High Tg Epoxy laminates are good for multi-layer PCBs operating in high temperature environments. For Lead-free PCB assembly, the industry prefers BT Epoxy, as these laminates offer outstanding mechanical, electrical, and thermal properties for multi-layer boards. For multi-layer flexible, high density, and rigid-flex circuit boards, the industry uses Polyimide laminates as this material offers very good mechanical, thermal, chemical, and electrical properties that advanced applications such as in consumer, automotive, aerospace, and military electronics require.
Read About: PROPER COMPONENT PLACEMENT ON PCBS
Rush PCB uses the most appropriate laminate for the application when fabricating PCBs for customers. For any type of PCB requirement, please contact Rush PCB today, or visit our website.