In the Printed Circuit Board (PCB) assembly process, the most important part is the deposition of solder paste on the board. The aim of the process is to deposit an accurate amount of solder paste onto each pad on the PCB. The operator achieves this by screen-printing the solder paste through a stencil or applying it via a jet printer. According to Rush PCB, this part of the process requires careful control, as it accounts for many of the assembly defects.
All items under use affect the printing quality of the solder paste. These include:
- The SMT Solder Paste
- Printed Circuit Board
- Printing Equipment and Fixture
- The Printing Process
- Production Environment
- Professional Quality of the Operator
The SMT Solder Paste
The three main factors affecting the print quality of the SMT solder paste are:
- Viscosity of the Solder Paste
- Uniformity and Size of Particles in Solder Paste
- Thixotropic Index and Metal Content of Solder Paste
One of the most important factors affecting the print quality is the viscosity of the solder paste. If the viscosity is too high, the solder paste will not pass easily through the opening of the stencil, and the deposits will not be complete. On the other hand, solder paste with low viscosity will flow easily and collapse, thereby affecting the resolution and flatness. Rush PCB recommends measuring the paste viscosity using a precision viscometer.
Along with the viscosity, the solder paste must be tacky to the right extent. If the solder paste is not sticky enough it will not roll on the stencil during printing. As a result, the solder paste will not fill the stencil opening, and there will be inadequate amount of solder paste deposited on the pads.
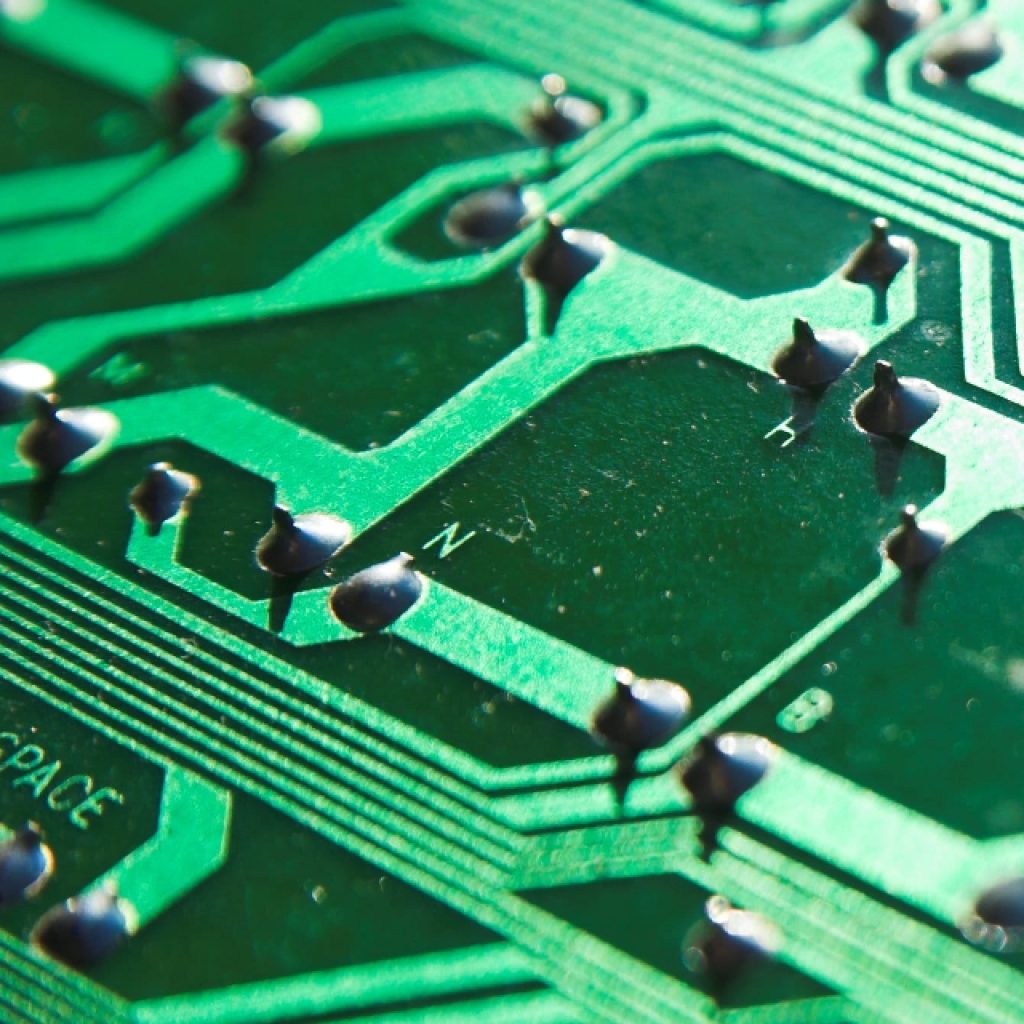
The printing performance also depends on the uniformity and size of particles in the solder paste. This includes the shape, diameter, and uniformity of the particles making up the solder paste.
The thixotropic index and metal content of the solder paste determine the thickness of the solder after it has solidified. An increase in the metal content tends to increases the thickness of solder. However, beyond a given viscosity, increasing the metal content leads to an increasing tendency for creation of solder bridges.
Printed Circuit Board
A flat printed circuit board offers the best print quality of solder paste deposit. Any camber or bow in the board prevents the stencil from resting flat on the board, resulting in uneven deposit of solder paste during the printing process. Rush PCB recommends proper registration of the stencil with the PCB before every printing process for accurate deposition of solder paste on the pads.
Printing Equipment and Fixture
The quality of the stencil and the squeegee affect the printing quality of the deposit of solder paste on the board. The greatest influence is due to the thickness of the stencil, as it must follow an optimal relationship to the size of the openings in the stencil. The thickness of the stencil along with the area of the openings define the volume of solder paste deposited by the printing process.
A thick stencil with large openings will deposit a higher volume of solder paste and this could lead to solder bridging. Conversely, inadequate solder paste volume deposited by a thin stencil with small openings might lead to dry soldering.
The smoothness of the walls of the openings in the stencil and their shape also affect the quality of solder paste the stencil releases during printing. The outer dimensions of the opening must be compatible with the shape and size of the pads on the PCB, as it affects the precision of the solder paste deposit.
The hardness of the squeegee is another factor influencing the quality of printing. The process may use a metal squeegee or a non-metallic one. While the non-metallic squeegee is much thicker than a metallic squeegee, their hardness affects the way solder paste moves across the stencil.
Read About: WHAT IS A SOLDER JOINT?
The Printing Process
Several parameters of the printing process affect the quality of printing of the solder paste. These include squeegee parameters, pressure, printing speed, printing stroke, printing angle, separation speed and cleanliness of the stencil. All the above parameters influence the amount of solder paste deposit and its quality.
The speed at which the operator draws the squeegee across the stencil determines the amount of time available to the solder paste to roll into the openings in the stencil and then onto the pads on the PCB. Usually, the operator must optimize the speed depending on the solder paste in use and the size of the openings in the stencil.
The pressure on the squeegee is an important factor, and the operator must maintain adequate pressure spread equally along the squeegee length to ensure the stencil has a clean wipe. While insufficient pressure can smear the solder paste on the stencil and result in incomplete transfer to the PCB, too much pressure can cause scooping of the paste from large openings, along with excessive wear on the stencil.
Scooping of paste from large openings in the stencil also depends on the angle of the squeegee blade when the operator is printing—increasing the angle leads to higher amounts of scooping, leading to less solder paste deposits.
Production Environment
Temperature and humidity play a major role in affecting the quality of printing. Before the printing process begins, the operator must bring up the temperature of the solder paste to the room temperature. Rush PCB recommends following the specifications provided by the solder paste manufacturer for room temperature and humidity required for a specific solder paste brand for achieving optimum results.
Read About: TRENDS IN PCB MATERIALS
Professional Quality of the Operator
As solder paste printing is an important step in the assembly process, the operator must have adequate training and experience to achieve the best operational quality. Rush PCB has special operators for the solder paste screen printing process, and they undergo training and evaluation according to international standards.
For all your PCB requirements, Rush PCB offers a professional approach to give you the best quality of PCBs. Please contact Rush PCB today, or visit our website with all your PCB requirements.