Rush PCB recommends using multi-layer rigid flexible printed circuit boards for reducing the weight and size of the assembly, improving circuit board reliability, PCB assembly flexibility, avoiding wiring errors, and achieving three-dimensional assembly under different conditions. As rigid-flex boards are thin, light, and flexible, and they meet the interconnection technology of integrated circuits, the communication and electronics industry values them highly and uses them widely.
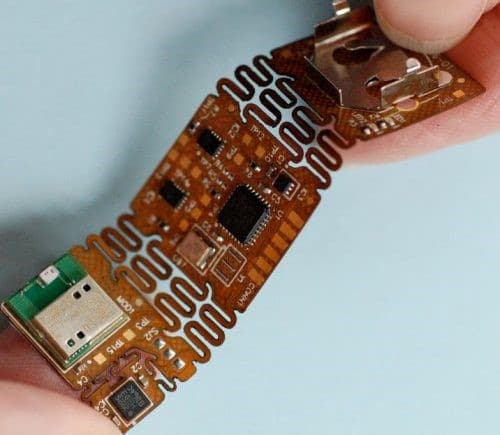
The industry requires flexible PCBs in single-, double-, and multi-layered boards, with stringent requirements of thin line width and spacing, for SMT or Surface Mount Technology and for other technologies. Fabricating rigid-flex PCBs requires special attention to material characteristics of the flexible substrate, substrate processing, dimensional stability, electroplating and metallization of small holes, decontamination, and surface coating for protection and reliability.
Types of Flexible PCBs
Depending on their structure, it is possible to classify flexible PCBs into the following categories:
- Single-Sided Flexible PCB
- Double-Sided Flexible PCB
- Multi-Layered Flexible PCB
- Single-Sided Rigid-Flex PCB
- Double-Sided Rigid-Flex PCB
- Multi-Layered Rigid-Flex PCB
Selection of Materials for Rigid-Flex PCBs
Selection of materials for rigid-flex boards is a very important process, as the material selection affects the production and performance of the PCB directly. This includes insulating substrate material, adhesive, copper foil layer, and cover layer. The primary material for flexible PCBs is a flexible insulating film that functions as a carrier with excellent electrical and mechanical properties.
Rush PCB prefers the use of Polyester and Polyimide material for the interlayer adhesive layer in a multi-layer flexible board, which helps to overcome dimensional instability problems. Other types of substrate material are also available such as PEN and thin FR-4.
Control of Key Production Processes
Further processing of rigid-flex boards follows patterns manufacturers use for multi-layered high-density rigid boards. However, some design requirements of the rigid-flex PCB are different because of the flexible nature of the PCB materials.
Transfer and Cleaning Processes
Rush PCB uses internal monolithic graphics transfer process. This is an important process for generating high-density, thin-line printed boards. However, as the PCB material is soft and thin, surface treatment becomes difficult. Cleanliness and roughness of the copper foil affects the adhesion to the dry film and therefore, the generation of fine lines. Mechanical cleaning is not suitable as the pressure may cause the substrate to deform, fold, or telescope. Rush PCB prefers to use electrolytic cleaning methods instead.
Electrolytic cleaning methods ensure not only the surface cleanliness, but also make sure the copper surface is adequately rough by using micro-etching methods. This process is specifically beneficial for fabricating very thin lines and spacing. Special attention is necessary for the acid etching process and the etch-rate for ensuring proper width and spacing of copper traces.
Read About: CONCEPT & MECHANICAL DESIGNS OF FLEX & RIGID-FLEX PCBS
Positioning of Flexible Layers
As moisture absorption rate of the Polyimide material is high, it leads to poor dimensional stability of the substrate material. This is especially noticeable after wet processes, and in different conditions of temperature and humidity, leading to severe deformation and difficulties in alignment of layers in multi-layer PCBs.
To overcome the above difficulties, Rush PCB uses alignment holes to align each layer properly. By lining up the alignment holes, it is possible to eliminate errors from stretching and deformation of inner layers during wet treatment. After lamination, Rush PCB uses X-rays to determine offsets during drilling, as it makes drilling much more accurate.
The offset is important because of the material and environmental characteristics of Polyimide. Aligning the outer film with reference to the offset improves the degree of alignment.
Assembling Rigid-Flex PCBs
Flexible PCBs tend to deform because of their thinness and light weight. Therefore, assemblers cannot directly assemble them on SMT manufacturing lines like they do for rigid PCBs. The usual practice is to fix the flexible PCBs on trays or rigid carriers so that it becomes possible to deal with them just like rigid PCBs. The board carrier must be consistent, flat, and accurate for positioning to maintain product quality.
As rigid-flex PCBs are of relatively higher cost compared to rigid boards, most OEMs apply them for connecting between modules based on concern for product cost. Therefore, the number of components they assemble on rigid-flex PCBs is relatively low, resulting in low assembly density.
Most OEMs use rigid-flex PCBs where the area of the board is small, coupled with low assembly density. To improve the assembly efficiency, assemblers use rigid-flex PCBs in panels, and separate them by punching after completing assembly.
As they deform and damage easily, assembly of flexible PCBs requires use of several auxiliary fixtures. This includes fixtures for board baking, trays for carrying boards, fixtures for conducting electrical tests, fixtures for functional testing, and fixtures for cutting the boards.
Read About: RISK FACTORS FOR FLEXIBLE PRINTED CIRCUIT BOARDS
Product Quality Requirements
As flexible PCB applications require them to bend repeatedly, their accuracy must be under control, and the components on the flexible PCB must meet the application environment demands. Therefore, assembling flexible PCBs requires higher cleanliness, soldering reliability, and anti-static precautions as compared to that required by regular rigid PCBs. In addition, due to a higher prevalence of RoHS and Lead-free manufacturing, flexible PCB manufacturing and assembly must be capable of withstanding higher technical challenges.
Cost of Flexible PCB Assembly
Cost of flexible PCB assembly is higher compared to that of regular rigid PCB assembly. This is particularly true as a result of requirements of fixtures, low rate of equipment utilization, long manufacturing periods, high demands of accessories and staff, and higher demands on product quality and manufacturing environment.
Conclusion
As applications of flexible PCBs increase and their technology improves, optimization of manufacturing processes will lead to a gradual decrease in cost of PCB fabrication and assembly. This in turn will further lead to a wider range of applications for flexible PCBs.
Rush PCB offers full turnkey PCB assembly, as we have a rich experience in handling flexible PCB assembly projects. Please reach out to us for discussing your projects involving flexible circuits and request for a flexible PCB assembly quote.