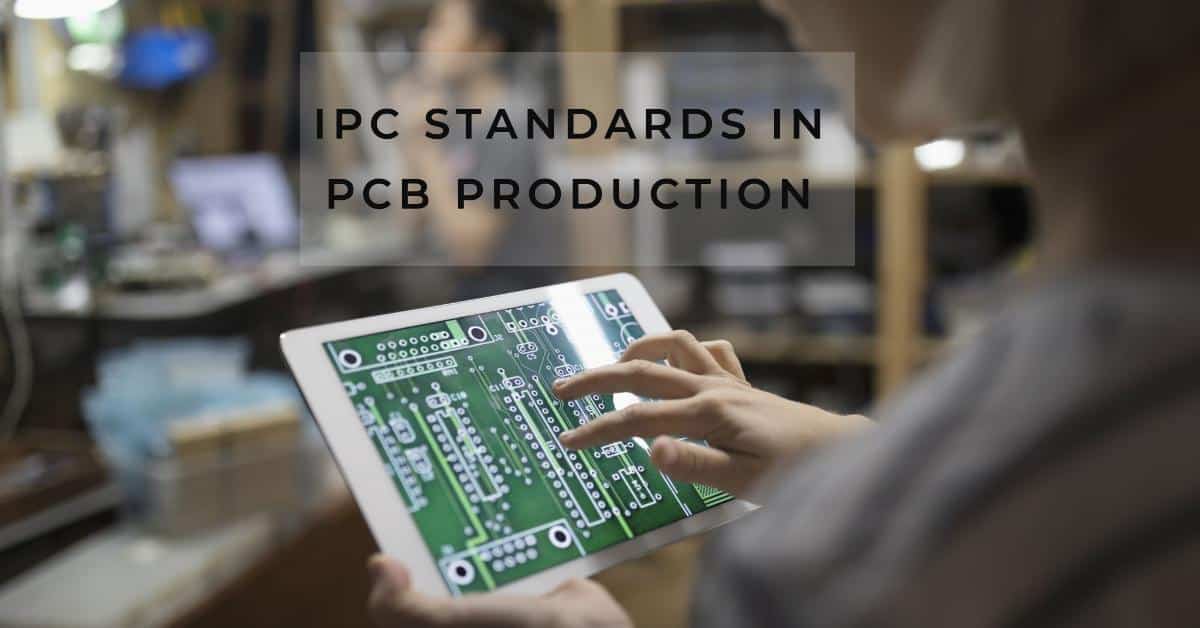
The Association Connecting Electronics Industries, now known as the Institute for Printed Circuits or IPC is a trade association for the electronic interconnection industry. It authorizes high-quality electronics by developing standards that drive the success of the electronic industry worldwide.
Introduction
The IPC consists of over 3000 companies that design, manufacture, and assemble boards for equipment ranging from consumer, wearable electronics and telecommunication, to healthcare and automobiles. Members of the IPC are from various facets of the electronics industry such as PCB manufacturers, OEMs or original equipment manufacturers, suppliers, and assembly service providers.
IPC and the electronics industry work together to identify industry challenges, and its members collaborate in providing adequate solutions. IPC gathers the latest information related to the industry of electronics manufacturing and outlines appropriate standards for best practices.
IPC-developed standards apply to all stages in PCB design, manufacturing, production, assembly, and testing. According to Rush PCB Inc., these standards are not simply guidelines — they are the very essence of quality in the PCB manufacturing industry. They ensure products that the electronics industry manufactures meet the highest quality and reliability criteria while maintaining consistency across all manufacturers and regions. Businesses involved in the production and assembly of electronic PCBs, components, and systems find that following these standards is crucial.
Key IPC Standards for PCB Production
Topics | IPC Standards | Description |
Terms and Definitions | IPC-T-50 | Listing of terms & Definitions in the standards. |
File Formats and Product Documentation | IPC-2581 & IPC-2610 Series | Specifications for sharing electronic product data and documentation. |
Design and Land Patterns | IPC-2221 Series | General design principles & land patterns for board layouts. |
Substrates and Materials | IPC-4101 Series | Specifications for PCB base materials and substrates. |
Quality and Reliability | IPC-6011 Series | Foundation for quality & reliability in PCB manufacturing, covering rigid, flex, and rigid-flex boards. |
Acceptability Criteria — Finished PCBs | IPC-A-600 Series | PCB categories based on intended use, required reliability, & criteria for acceptability of finished PCBs. |
Requirement Criteria — Soldered Electronics & Assemblies | IPC-J-STD-001 IPC-AJ-820 IPC-HDBK-001 |
Requirement Criteria for Soldered Electronics & Assemblies. |
Acceptability Criteria — Soldered Electronics & Assemblies | IPC-A-601 | Acceptability of Soldered Electronic Assemblies |
Requirements and Acceptance — Cable & Wire Harness | IPC/WHMA-A-620 IPC-HDBK-620 IPC-D-620 |
Requirement and acceptability criteria for cable & wire harness assemblies |
Acceptability Criteria — Electronic Enclosures | IPC-A-630 IPC-HDBK-630 |
Acceptability for manufacturing, inspection, and testing of electronic enclosures |
Reporting Format — Material Declaration Data | IPC-1752A | For exchange among designers, distributors, and manufacturers or bulk materials, components, assemblies, and products. |
Current Carrying Requirements — Copper Traces & Planes In PCB | IPC-2152 | Useful in PCB design |
Requirements of Generic Design and Performance in PCBs | IPC-2221 | For component mounting and/or interconnecting structures on PCBs |
Guidelines for via protection | IPC-4761 | For dependability, manufacturability, and quality of vias in PCBs |
Design guidelines incorporate IPC standards, and effective checklists can verify them throughout the development process. Customers prefer products that not only guarantee high performance but also user safety. Adhering to IPC standards certifies a PCB product to be of excellent quality.
Comparison with Other Industry Standards
UL Standards
Standards from UL or Underwriters Laboratories focus primarily on safety. IPC standards encompass both the quality and reliability of PCBs, electronic components, and their assemblies and are more comprehensive.
ISO Standards
ISO standards like ISO 9001 provide a broad coverage of the various aspects of quality management systems. On the other hand, IPC standards focus specifically on PCB and electronic assemblies.
Essentially, IPC standards, rather than being mere guidelines, are the backbone of innovation and quality in the PCB industry. They offer a distinct focus and provide a more specialized approach in comparison with other industry standards. For anyone involved in electronic design and manufacturing, the IPC standards are crucial and compelling.
Why Adhere to IPC Standards?
Adhering to IPC standards in the PCB manufacturing industry is not only for compliance, but it is a strategic move that carries with it a multitude of benefits—elevating the entire manufacturing process—from design to the final product, such as:
Product Quality and Reliability
Consistency & Enhanced Product Value
Adhering to IPC Standards ensures PCB manufacturing uniformity, ultimately leading to products consistently meeting high-quality benchmarks and customer satisfaction. This not only contributes to the consistency of the product but also its overall value in the market.
Durability
Adhering to IPC Standards significantly enhances the reliability and longevity of products, reducing the likelihood of malfunctions and failures.
Improved Communication
As all the involved members follow the same IPC standards, groups find it easier to communicate. They can avoid ambiguity during communications, while the common jargon helps in setting a clear interpretation.
Lower Expenses
By adhering to IPC Standards, manufacturers can improve their supply-chain efficiency. Not only does this help in reducing resource requirements, but it also substantially lowers the cost of production.
Seamless Workflow
With all team members following IPC Standards diligently, the possibility of delays and faults is reduced significantly. For a PCB product, this translates to a smoother flow in its development, production, and assembly processes.
Environmental Sustainability
As IPC Standards often advocate using environmentally friendly materials, they also promote sustainability in manufacturing. Optimization of manufacturing processes by following IPC Standards helps in minimizing waste, thereby contributing to eco-friendly practices.
Importance of IPC Standards in PCB Production
Adherence to IPC Standards streamlines the entire process beginning with design, through manufacturing, to testing. They ensure a seamless transition from design to manufacturing. By adhering to IPC standards, designers create PCB designs compliant with current technologies and adaptable to future advancements.
In the PCB production process, IPC Standards are an integral factor. They aid in the PCB design process, offer guidelines in material selection, influence the selection of design software, impact the manufacturing process, and help in adapting to future emerging technologies. This ensures that PCBs designed and produced are efficient, reliable, and simultaneously, forward-looking and adaptable to innovations in the future.
QA Processes in PCB Production
During PCB production, a series of comprehensive checks at various stages are necessary for quality assurance. This involves raw material inspection, fabrication process monitoring, and finished product testing and inspection.
IPC Standards serve as a guideline for such quality checks, ensuring each product meets the requisite specifications for board thickness, copper weight, trace width, soldering quality, and more.
Testing Protocols and Procedures
Electrical
Specific procedures are available in IPC Standards that provide detailed electrical testing, ensuring each assembly functions properly according to its intended operational conditions.
Environmental
IPC Standards also offer protocols for environmental testing, including checking structural integrity, durability, and thermal resistance under different environmental conditions.
Complying with IPC Standards
Steps to compliance include understanding the standards, implementing them, and obtaining the certification.
Understanding the Standards
This is the first step in compliance. The requirement is to gain a comprehensive understanding of the relevant IPC Standards, correlate them to linked Standards, and interpret them correctly for meeting specific PCB projects.
Implementation of the Standards
This step involves properly incorporating the understood and interpreted standard into all stages of the PCB design and manufacturing process, beginning with the initial design and ending with the final quality checks.
Obtaining the Certification
There are two stages in this step:
Understanding the Certification Requirements
To obtain an IPC certification, it is necessary to perform a detailed evaluation of the company’s processes and products. This involves understanding the requirements of the certification process.
Significance of the Certification
The IPC certification, once obtained, is not simply a badge of honor. Its significance lies in continued commitment to reliability and quality, enhancing the trust and credibility of partners and clients.
Conclusion
In our through the intricate world of IPC Standards in PCB manufacturing, we, at Rush PCB Inc., cannot emphasize enough that these standards are not mere guidelines, but form the very foundation of innovation and quality in the industry. Embracing the IPC standards is not only a measure of compliance, but a commitment to quality, and a pledge to uphold the highest possible standards of efficiency and reliability of PCB products. The electronics industry is constantly evolving, and it is necessary and crucial to stay competitive while meeting the ever-changing requirements of the market. Adherence to IPC standards allows just that.
FAQs
What is the IPC Class of PCBs and which standard addresses it?
The IPC-A-600 series defines three classes of PCB assemblies:
Class 1, for consumer and general electronics
Class 2, for home appliances, laptops, and service-oriented electronics
Class 3, for mission-critical electronic products.
Is it necessary to understand all IPC Standards?
IPC Standards have many sections, not all sections apply to every design, and not all of these are critical for PCB designers/manufacturers. Select the standard/standards best suited for your application.
Which IPC Standard should I follow for component footprints?
IPC-7351 offers standards on land patterns for component footprints. Component manufacturers and designers follow these standards to ensure compatibility and manufacturability on circuit boards.
Apart from IPC, what other standards apply to military products?
Military products require adherence to IPC Class 3 for reliability. Other standards important for military products include SAE, FAA, MIL, and ISO.
Is there any IPC Standard that defines the relationship between trace width and current capacity in PCBs?
You can refer to the IPC-2152 Standard. It recommends the relationship between trace width, copper weight, and current capacity in PCBs.