Most industries use DFMA or Design for Manufacturing and Assembly techniques to mainly minimize product cost through improvements in design and process. Two procedures make up the term—Design for Manufacturing (DFM) and Design for Assembly (DFA)—with many differences and similarities between the two. Rush PCB explains why DFMA techniques are essential in the PCB industry.
DFM & DFA — Differences
While DFM strives to optimize the manufacturing process, DFA seeks to optimize a part or system assembly. To put that in simpler terms, DFM is concerned with reducing overall production costs, but DFA is concerned only with reducing the product assembly costs. In other words, while DFM helps to minimize the complexity of manufacturing operations, DFA helps to minimize the number of assembly operations.
DFM & DFA — Similarities
Both DFM and DFA procedures help in reducing material, labor, and overhead costs. In striving to reduce costs, both technologies tend to utilize standards. Both procedures strive to shorten the time involved in the development cycle of a product.
Terminology
The industry commonly refers to the two—Design for Manufacturing and Design for Assembly—as a common methodology, and DFMA or Design for Manufacturing and Assembly as the common terminology. This is because the design processes exert a much greater influence over the price, quality, and cycle time of a product as compared to that from the manufacturing processes.
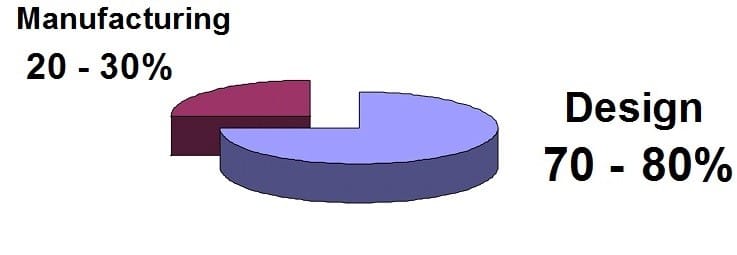
Sequence of Analysis
Rush PCB recommends adoption of both DFA & DFM procedures early in the design cycle. In general, the sequence of analysis the industry follows begins with DFA procedures during the concept design of a product, where the designer optimizes the design for parts count and assembly sequence. The DFM procedure follows next, where designers tend to optimize the design for production readiness. After this, the designer takes up the detailed design.
DFMA Procedures for PCBs
The traditional disciplines of DFA and DFM have strict and distinct methodologies, with specific focus on yield and cost. However, the PCB industry treats the terms rather differently.
In the turnkey environment of PCBs, it is usual for PCB manufacturers to refer to DFM procedures as the stage where they asses the design of a PCB from the point of view of manufacturing it. Likewise, they refer to DFA procedures as the stage for assessing the assembly of various components and the PCB.
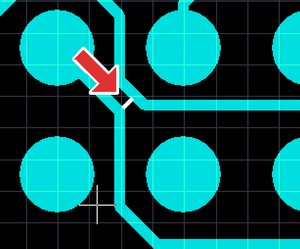
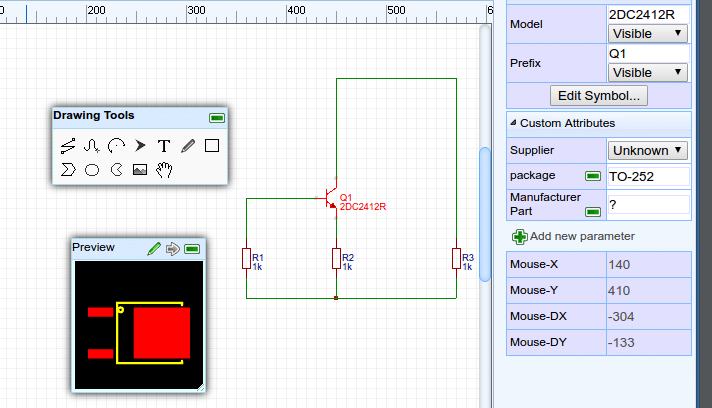
Therefore, although in its basic sense DFM ensures that a PCB is manufacturable, while DFA ensures it is possible to assemble the PCB and its components, there is no specific emphasis on cost reduction or yield maximization. Therefore, it is pertinent to raise the question, why is DFMA important for the PCB industry?
Importance of DFMA for the PCB Industry
DFM is necessary from the onset of design, as the aim is to manufacture a working PCB. DFA is also necessary from the onset, as the aim is to reduce complications while assembling. Therefore, manufacturers need DFM as it allows them to decide whether they can at all fabricate the PCB, while assemblers need DFA as it allows them to assess whether they can assemble the PCB easily, with difficulty, or not at all.
In the turnkey PCB assembly process, where the assembler essentially gathers all the components for assembling the board, DFMA is an essential factor. This is because, in the PCB design scenario, one small mistake can disrupt the chances of a product making it to the market in time.
Considering there are so many parts that come together for assembly on a PCB from various manufacturers and with varying degrees of reliability, designers have a tough time with the complexity, and they can easily overlook the margin for error involved with each footprint. Therefore, a qualified practicing engineer conducting DFA checks on a PCB can be saving valuable time for the enterprise.
The PCB designer hands over several documents that specify the manufacturing process for fabricating the board. These are mostly Gerber files, with details of individual layers and drill holes. It is necessary for the manufacturer to use DFM checks to verify the Gerber files are accurate. For instance, the input files may have asked for a via in an impossible position, or a net may be missing in the routing. While the PCB is not manufacturable in the first case, the board, although perfectly manufacturable in the second, will be useless after fabrication.
Rush PCB offers Design for Manufacturing and Assembly for all PCB assembly orders. Through our DFMA processes, we strive to remove nasty surprises that may hold up your product. We have experienced engineers on our team with extensive hands-on experience of product development, and you can rest assured they will remove the road-blocks in time to give you peace of mind. Of course, our DFMA procedures are optional, and you can either skip the review or allow us to conduct it. However, we strongly advise going for our DFMA review, as this procedure helps to avoid expensive mistakes, saves time, and paves the way for achieving better designs in the future.