PCB manufacturing and PCB assembly are two different industry fields, conforming to different IPC and other standards. While PCB manufacturing concerns the fabrication of the bare circuit boards, PCB assembly concerns the placement of various components on the bare board and soldering them.
As a leading turnkey PCB manufacturer and assembler, Rush PCB handles all types of boards like rigid, flex, rigid-flex, HDI, and many more. Manufacturing and assembling PCBs involves several complicated processes. Several factors influence the quality, durability, and cost-effectiveness of both the bare board and the assembled PCB. Based on our enormous industry experience and knowledge of PCB manufacturing and assembly, we offer a few tips to make the PCB assembly process a success.
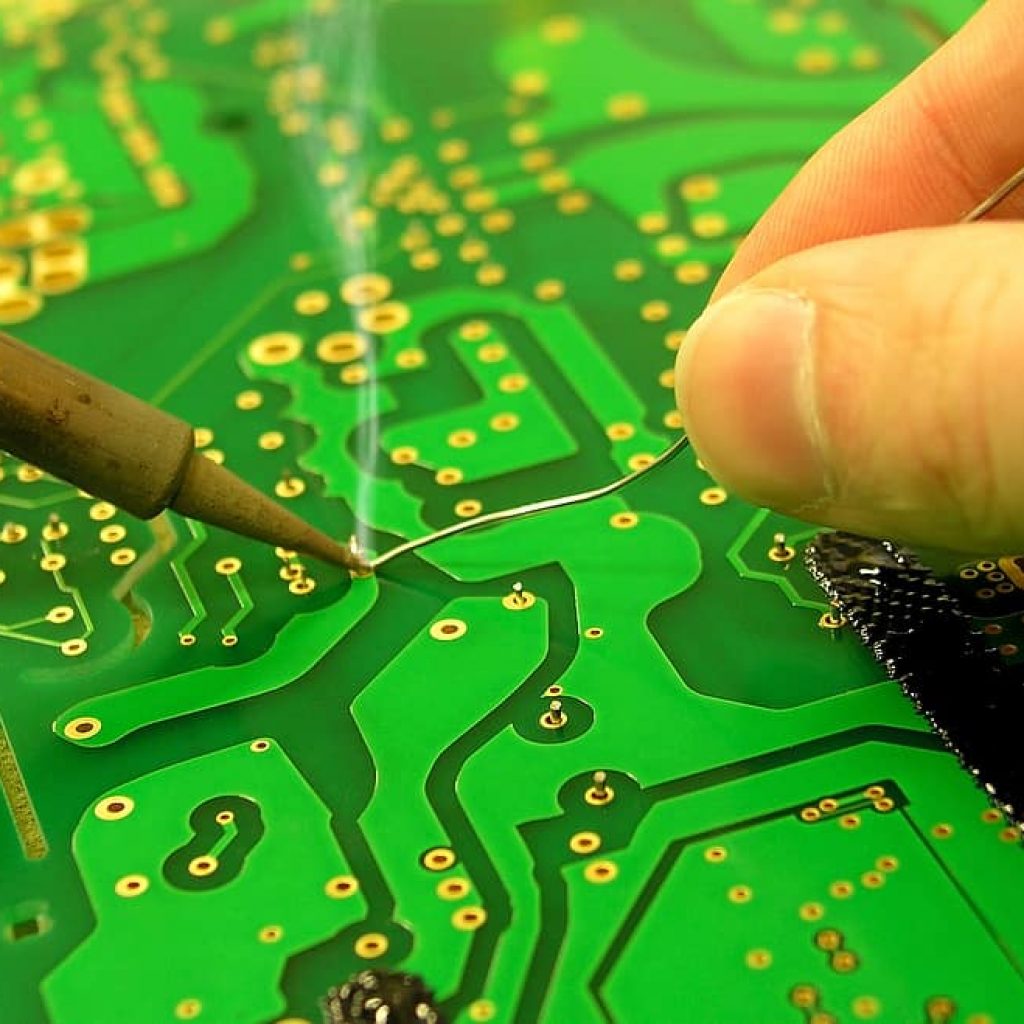
A successful PCB assembly project involves three basic ingredients:
- The Bare PCB
- The Components
- The Assembly Processes
A shortcoming in any of the above ingredients can derail the project. Let us look at each of them in turn.
The Bare PCB
Rush PCB creates excellent prototype printed circuit boards for our customers. The process of transforming a design from the schematic to the bare prototype board is a complex one.
Many of our clients use innovative proprietary technologies in their PCB orders. While the client’s engineers are familiar with the technologies they are using, as a manufacturer we need to know why they are using these technologies and the way it solves their problems.
While handling orders from customers that use patented technologies, the depth and clarity of the documentation affects our speed of execution and the quality of the prototype we are manufacturing. Therefore, thorough documentation is essential to allow us to complete our projects without resorting to revisions. To manufacture the bare PCB, we require:
A Complete Netlist: This is to ensure the operator knows all electrical connections that exist between the various components on the board. Apart from the electrically connected terminals of components, the netlist must list all the floating or unconnected terminals as well.
Gerber Data and Defined Apertures: Undefined apertures with Gerber data can lead to production delays. Gerber data processing requires a clear definition of all apertures. If the customer has not defined the aperture, the operator must define it manually, and that involves a risk of error and hence a delay in execution.
Actual Size Board Outline: An actual 1;1 board outline along with the Gerber data or ODB++ format helps us in understanding how we must assemble the various parts and components. Providing an accurate outline helps in developing routing programs for the board’s profile, while allowing our engineers add critical dimensions when processing.
The Components
As a leading turnkey assembler, Rush PCB regularly orders, confirms, tracks, verifies, prepares, and identifies electronic components. This is a time-consuming and tricky process. If the customer is supplying the components, we recommend you follow the simple steps below for a successful PCB assembly—for a full turnkey process, Rush PCB also follows them:
Order Only from Authorized Distributors: To avoid using counterfeit components, Rush OPCB recommends ordering only from known authorized distribution source, or directly from the manufacturer. The order must also cover the consigned kit requirement for the PCB project.
Confirm the Order: Until the actual delivery takes place, confirm from the source the date of delivery, the type of component, and the tracking mechanism. Keeping a track of the order is a necessary step and avoids missing shipments at critical moments.
Verify the Order: As materials arrive, it is necessary to verify what you have received is what you had ordered. Compare and confirm with the datasheet of the manufacturer to verify the markings and values pertain to the ordered components. All examination and verification processes must take place in ESD safe zones and operators must follow ESD safe handling processes.
Maintain Traceability: It is important to maintain the traceability of the components in case there is a performance issue later. We recommend retaining the manufacturing information and the original lot code from the shipping packages for each consignment for maintaining traceability. This information is also useful for enlisting manufacturer support if necessary.
Make Kits for Assembly: Each assembly will have a consignment of components suitable for a PCB or panel. This includes reel preference, leader and trailer lengths, overages, and similar.
Identify the Components: For an accurate and efficient assembly, it is advisable to label the components clearly and legibly. The labeling must be consistent with the entry in the bill of materials, as this helps with audits. The label must also contain all necessary information.
As PCB assembly can contain thousands of components, the assembler must be careful in preparing the kit. Making a mistake on even a single component can lead to missing the deadline and reputation.
The Assembly Processes
We recommend our customer contact us at the beginning of their project and not at the end. As a leading turnkey PCB contract manufacturing supplier, Rush PCB would like to offer information about our capabilities for panel design and other modifications necessary for smooth PCB assembly and manufacturing processes.
Connecting with the contract manufacturer at the start of the design processes allows the designer to incorporate features that help the assembly process proceed without holdups. For this, we suggest following two processes periodically as the design progresses. These are Design for Assembly or DFA and Design for Manufacturing or DFM.
Design for Manufacturing: The DFM process allows the designer to assess the design of the PCB for optimizing its dimensions, materials, tolerances, and functionality. Designers can trim their overheads and improve the product quality by improving on pre-existing designs. Re-evaluating the design and processes can detect wasteful steps, and the designer can eliminate them before the production starts.
The DFM process helps to eliminate miscommunications between designer and contract manufacturer. The designer, when conceiving the product, can use the DFM process to make sure the contract manufacturer would have no problems while fabricating it.
Following the DFM process prevents costly changes and production delays.
Design for Assembly: To assemble the board efficiently, its design must take into account the constraints of the contract manufacturer. The equipment and processes the contract manufacturer uses mainly define these constraints. Collectively, these constraints form a bulk of the DFA guidelines. For ensuring the best assembly process, the designer must incorporate these guidelines from the initial design stages.
Capabilities of the Contract Manufacturer: It is important to assess the capabilities of the contract manufacturer before starting the design. For instance, the new design may be using SMT components and the present contract manufacturer can only handle through hole components. Therefore, the designer must either change the design or find a new contract manufacturer with suitable capabilities.
The designer must also assess the extent of the capabilities of their contract manufacturer. For instance, they must assess if the contract manufacturer can solder fine-pitch BGAs. This may also require the assembler to inspect the PCB using X-rays.
Conclusion Success in PCB assembly projects leads to reductions in time-to-market for the customer, while delays involve more expenses and loss of time for both the customer and the contract manufacturer. Rush PCB expects customers will benefit from our experience and follow the above processes for successful PCB assembly projects.