Eminent Printed Circuit Board (PCB) manufacturers such as Rush PCB offer two distinct types of service—PCB prototyping and standard PCB production. This is because electronic designs have historically followed a clear evolution. Engineers first make and create a design on a breadboard or computer to test its functionality. Then they prepare a board layout and test with prototypes. They incorporate changes to the design based on their tests and put the final version to production.
Earlier, technological barriers forced engineers to limit their PCB design to single and/or two-layer boards. However, with advancement in technology and requirements of the marketplace, creating multi-layer boards with more than 6 layers is the norm, and OEMs tend to use boards with higher density and smaller SMD components to stay competitive.
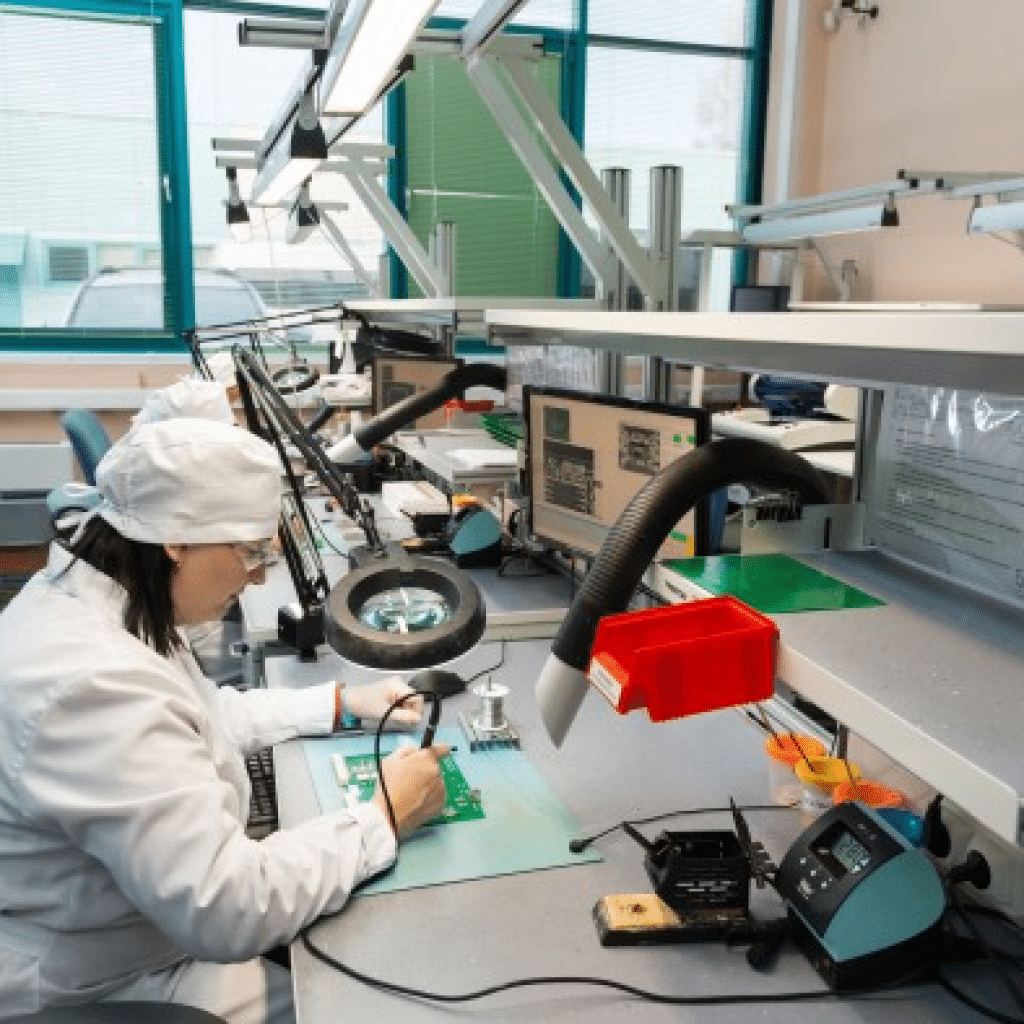
Engineers need to prove their concept with their design first before they commit the PCB design to mass production. This stage of design and manufacturing requires a concept that the electronic industry calls as prototypes. At this stage the engineers require a small batch of roughly ten boards made to the same standards and finish as that required by the final production boards.
For most PCB manufacturers this requirement is not cost-effective. That is because the work necessary for setting up the production sequence to make 1-10 prototypes requires the same labor-intensive steps that a quantity of 1-10000 would. However, Rush PCB has configured their production processes such that they can take up small batches of prototypes at very competitive rates for their customers.
Why PCB Prototypes?
Almost any electronic product requires a PCB to hold the electronic components in place and provide the electrical interconnections between them to allow the circuit to function as the designer intends. During the design process, the engineer must arrive at a cost-effective method to achieve the desired functionality. It may be necessary for the designer to select the most suitable material for the PCB, and prepare a Bill of Materials (BOM) for all the components that are necessary to make up the product.
At this stage, the OEM needs a qualified PCB manufacturer with whom they can discuss the requirements for the PCB materials and its manufacturing process. Both need to follow the process of Design for Manufacturing (DFM) so that the final PCB will function as intended. To do this, the manufacturer must be capable of offering a few prototype boards to the engineer to prove their design concept.
Engineers typically use prototype PCBs to iron out the design problems and improve the entire process for enhancing the product performance. However, they cannot proceed very far into this process unless they have PCBs that they can prove to be effective. This is where manufacturers help them with prototype PCBs.
Prototyping involves creating PCBs in a small batch using the same materials that the final boards will use. Using prototypes, OEMs ensure their design works as they intend, and they can assess whether it is worth doing a full standard production run. The prototyping stage goes through a fast but limited cycle so that the boards undergo a thorough inspection and test. Engineers utilize the prototyping stage for working out any kinks in their board design before they invest in large production runs. For designs that start from scratch, engineers prefer to go via the prototype PCB stage.
Standard PCB Production
Once the OEM has established that the basic prototype boards are working to their satisfaction, they can decide to enhance the design to include higher functionality. They may also incorporate changes necessary to the basic design to make it more efficient. Engineers usually take a little longer to test this final stage, as otherwise, they could end up wasting a lot of time and money for eliminating potential errors.
Standard PCB production provides more stringent production tolerances along with more advanced options. For instance, Rush PCB standard PCB services include free design for manufacturing (DFM) checking for detecting potential problems that may reduce the quality of the PCB.
Also Read: How to Choose Professional PCB Prototype Assembler
Advantages of PCB Prototype Services
Rush PCB offers PCB prototyping services that customers can use whenever they want. Our PCB prototyping services offer several advantages:
- Customers can make boards for design review, trial production, or quality inspection
- Multi-layer circuit boards with eight or more layers
- FR-4 grade boards
- Quality boards conforming to IPC1 standards
- All boards made with fast PCB turnover
Rush PCB recommends OEMs select the PCB prototyping service for performing functional testing of new products before committing to full production. Benefits from prototype PCBs are:
- Customers can test their design quickly and cost-effectively to correct any errors and design defects in the early stages
- Customers can achieve productivity goals much more quickly with a faster turnaround time, avoiding more expensive mistakes during full production
- Provides customers with more opportunities for iterating, innovating, and improving functionality
- Customers can order small batch production with minimum order quantity for testing quality and durability
- Lower production tolerances help estimate the performance of their PCBs
As soon as the prototype has proven their capability to meet the intended performance and quality requirements, design engineers may want to go for full production operation. Rush PCB then switches from PCB prototype services to their standard PCB services.
OEMs need to look for some basic criteria when evaluating prospective PCB manufacturers. These may include:
- Time to get a quote—quicker is better
- Availability of small production runs at reasonable prices
- Possibility of quick turnaround during iterations
- Standards followed by the manufacturer
To Prototype or Not to Prototype
Some OEMs may feel prototyping adds unnecessary cost to the product or it may result in longer time to market. Even when in a hurry, it makes sense to involve in prototyping, as prototyping is vital to a successful, smooth production run.
As no two products are the same, OEMs can have a flexible approach to making prototype PCBs. What an OEM requires from prototyping services depends on what they are trying to achieve. For instance, a product under development from start can present a more serious set of challenges than making small adjustments to an existing one does. Therefore, Rush PCB encourages OEMs to take a closer look at their approach towards prototyping for each of their projects.
For instance, the OEM may be already confident about the manufacturability of their project, and may simply be looking for validating a minor design change. It makes sense for the OEM to focus on speed, simplicity, and cost-effectiveness. They may want fast and economical prototyping for a favorable quality assurance and or tolerance testing for boards operating in harsh environments.
OEMs associated with a new design or project may prefer to place a higher priority on expert help. They may want a more consultative approach, as boards not meeting performance specifications require troubleshooting.
In prototyping, board complexity is always a huge factor, and is independent of the results the OEM is trying to achieve. Therefore, Rush PCB offers their Rapid Prototyping services that help in optimizing board quality, save expenses during production, and save OEMs the time to market. Rapid Prototyping has three approaches.
Approaches to Prototyping—Fast, Faster, Fastest
Quality is an important aspect, without which, cost-effectiveness and speed do not have any meaning. Whether the OEM is looking for fast, faster, or fastest prototyping, rapid prototyping services of Rush PCB always help in ensuring the best PCB quality.
Fast Prototyping
OEMs occasionally need expert help with their prototypes. Often, improvement projects and product development can be as complex as the PCBs involved. Even if the layout reviews do not indicate any issues, the design may not inspire full confidence. There may be unanswered questions involving requirements of panelization, assembly, materials, or finish.
Personal assistance from experts at Rush PCB can help remove such uncertainties. Rush PCB is always willing to step outside their established service offerings to provide custom solutions. We always try to integrate human interaction with technology platforms, tailoring the solution to customers’ requirements, but still maintain an expedited production pace.
Faster Prototyping
Our faster prototyping services strike a balance between complexity and velocity. Getting a board quickly from a manufacturer can be expensive. OEMs can save time and money by investing in both. Complex boards may need expert help with layout review.
OEMs should look for manufacturing partners who provide detailed comprehensive feedback on their PCB design before they produce the prototypes. This helps the OEMs as the reviews can unearth yield or reliability issues with the design. Such reviews also help to improve the integrity of the production schedule, while ultimately improving the quality of the boards.
OEMs may need to determine the service level they are looking for from the manufacturer. It helps to strike a balance between speed and performance validation. For instance, a 24-hour delivery of a board with a design flaw can delay the production schedule inordinately. Rush PCB recommends OEMs to invest time in the extra steps necessary to verify the reliability and functionality of their PCB, thereby allowing them to move forward to production with confidence.
Fastest Prototyping
Some projects may not require large amounts of money or time for prototyping. It could be that the PCB is not a complex one and the OEM is confident of designing and manufacturing it. For instance, the board may only be performing a basic function and does not require stringent layout restrictions, and or may not be subject to harsh environments.
Similar conditions apply to boards undergoing iterations from small design changes, and the OEM is looking for speed and cost-effective prototyping. Additionally, OEMs may not always have a healthy corporate R&D budget, and may be searching for a PCB manufacturer that can provide prototypes faster and cheaper.
Rush PCB advises caution with value-priced services as they may not provide equal service. Therefore, in addition to pricing, OEMs should also consider whether the manufacturer:
- Offers one-day lead times.
- Has design limitations such as maximum number of layers, shape limitations, maximum hole size, etc.
- Offers live customer support, 24/7/365.
Fastest prototyping can save the OEM time and money, provided they know when it is appropriate to use the service. They should also be confident that it will not compromise their PCB design or its functionality.
Conclusion
Rush PCB understands that PCB prototyping demands a continuous learning process, both for the manufacturer as well as the OEM. As each board is exclusive, the service level suitable for one board may not work for the other. Only with time and experience does one gain the intuition of the right approach for each case.