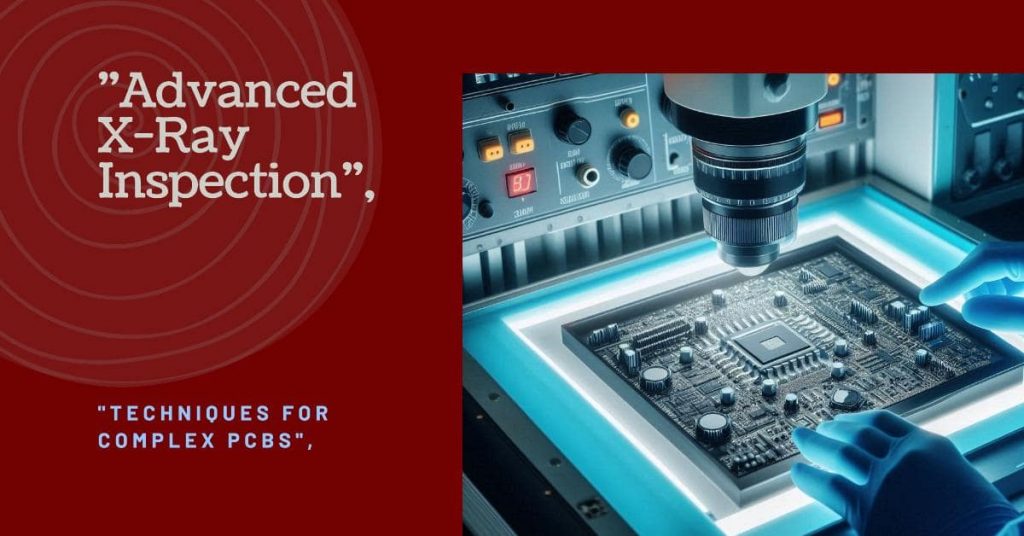
Introduction
During the past decade or so, PCBs or printed circuit boards have become extremely complex. They now have a high number of layer counts and very high component density, and their wiring is now more intricate. This has not only made defect detection increasingly critical but has also escalated the effectiveness of overall quality control to be that much more difficult. Traditionally, PCB manufacturers and assemblers relied upon methods using visual tools, moving on to manual microscopy methods, and then, to AOI or automated optical inspection. However, with an increasing trend towards PCBs with concealed solder joints, and more (fan out, capillary flow), these traditional inspection methods fall well short of their effectiveness.
The Need for Better Inspection Methods
While these traditional inspection methods have worked well for a while, in today’s trend towards PCBs with hidden or ‘concealed’ solder joints (and more, fan out and capillary flow), these methods are far less effective than they once were. Inspecting with X-rays enables them to pinpoint defects like open joints, bridges, and voids early while preventing field failures later. Rush PCB Inc. presents here a comprehensive guide to advanced X-ray inspection techniques for complex multi-layer PCBs.
What is X-Ray Inspection?
PCB Manufacturers are now using X-rays for examining subsurface conditions and internal features within PCBs in a non-destructive manner. They are utilizing the penetrative nature of X-rays and exploiting the PCB’s differential absorption characteristics for X-rays.
High-frequency electromagnetic waves with small wavelengths are called X-rays. They have such high energy, they can penetrate solid objects. As PCBs have natural variations in material thickness and density across the board, they absorb X-rays differentially. The resulting image projection is, therefore, encoded with the details of the internal structure of the PCB, and reveals defects.
How X-Ray Inspection Works for PCBs?
The X-ray inspection system principally has a source for generating X-rays. There is a manipulating system to hold the PCB and a detector array. Lastly, there are processing electronics for producing the sample images for defect analysis. The process is as follows:
- X-rays are generated by the source and all beam is focused on the PCB sample by a collimator.
- The operator uses the manipulator to position the board precisely to enable scanning of the board’s cross-section or its perspectives.
- Component materials and dense solder joints absorb X-rays more than the resin/substrate materials do. This results in an X-ray pattern of shadows falling on the detector.
- The detector processes this shadow pattern to produce a digital 2D or 3D image representing the internal structure of the PCB.
- Additional image processing techniques can enhance and reconstruct the image to aid visualization of defects.
- These images are examined by operators while viewing the inspection monitors to identify open joints, voids, cracks, and shorts.
The X-ray inspection is a non-contact method to detect hidden flaws in PCBs that manual inspection checking methods frequently miss.
How X-Ray Inspection Works for Components?
The X-ray inspection method is an extremely valuable tool for inspecting components. Various components that may be effectively inspected are as follows:
- CSP/BGA Packages
○ Verification of solder balls hidden below the package body.
○ Identifying insulation issues, open joints, shorts, and voids below the package body.
○ Identifying any trace damage or pad lifting under the package body.
○ Looking for damaged or cracked silicon die inside the package. - DFN/QFN Packages
○ Inspection of J-lead solder joints hidden below the package body.
○ It will detect lifted pads, inadequate wetting as well as solder voids under the package body.
○ To confirm package lead alignments with pads. - Special IC Packages
○ Inspection of solder joints hidden below packages like PLCC, QFP, SOIC, uBGA.
○ Detecting skewed parts, tombstoning, shorted pins, etc.
○ Confirming slotted pads are adequately filled with solder.
○ Checking for cracks or die damages. - Connectors
○ Checking array solder joints hidden below the connector body.
○ Verifying the quality of manual, wave, or selective and reflow soldering.
○ Locating bent or improperly seated sockets or pins. - Passive Components
○ Inspecting circumferential solder joint connections.
○ Detecting skewed, floating, tombstoned capacitors and resistors.
○ Detecting missing or incorrectly placed passive components.
Types of X-Ray Inspection Methods
Basically, the X-ray imaging method creates a two-dimensional representation of a PCB. However, by combining multiple 2D scans from various viewing angles, it is also possible to produce a 3D visualization.
- 2D X-Ray Inspection
This is the most basic method manufacturers use widely for PCB inspection. It captures a single image of the PCB in two dimensions from a fixed angle. The coarse defect detection capability of the 2D X-ray inspection method is adequate for the detection of large solder voids or missing components but is not sufficient to detect more critical issues. - 3D or Oblique View X-Ray Inspection
This method involves capturing X-ray images of the PCB from various angles. Typical angles used vary from 30 to 60 degrees. Manufacturers combine these images to form a significantly enhanced 3D view of the internal structure of the board. This allows the detection of defects that the single 2D image can miss. - CT or Computed Tomography X-Ray Inspection
This is an advanced technique in comparison to the two before it. This method captures a series of images while the PCB rotates 360 degrees. The images are processed by computer software that creates a detailed three-dimensional reconstruction of the board’s internal structure. Manufacturers use CT X-ray inspection methods specifically for examining multi-layered complex PCBs to identify defects that other methods cannot detect. - Automated and Manual X-Ray Inspection Methods
For low-volume production of PCBs, manufacturers rely on manual X-ray inspection methods, while they mainly use automated methods when inspecting PCBs in high volumes. By contrast, manual X-ray inspection methods depend on the experience and expertise of trained operators and the automated method employs advanced algorithms for image analysis to search for anomalies and defects in the images. The following table offers a comparison between the two methods:
Manual X-Ray Inspection Method | Automated X-Ray Inspection Method |
Relies on the experience and expertise of the operator | Relies on advanced software algorithms |
Low speed and low throughput | Higher speed and high throughput |
Higher nuanced and context-aware analysis | Improved consistency and repeatability |
Higher labor costs | Lower labor costs |
A human operator can miss subtle defects | Higher resolution defect detection even for complex designs |
Low upfront investments | Higher upfront investments |
Low maintenance | Higher maintenance and updates |
Integrating PCB X-Ray Inspection in the Manufacturing Process
Its effective integration within the manufacturing process is needed to maximize the benefits of the PCB X-ray inspection methods. The PDCA cycle is the most effective for organizations following an international QMS or Quality Management System. It involves:
- The PLAN Stage
○ At this stage, we decide how often the testing would be required; should it be for every board or a sampling of a certain batch will suffice. - The DO Stage
○ At this stage, it finds out where along the manufacturing process the X-ray inspection should take place, for example, right after fabrication, after reflow or after final assembly. - The CHECK Stage
○ It is necessary at this stage to decide and establish clear criteria to classify and report the defects. - The ACT Stage
○ At this point, we need to apply corrective and preventive action to resolve the defects we find.
By properly planning and executing the above stages, manufacturers can ensure the X-ray inspection method delivers maximum value for process improvement and quality control.
Benefits of X-Ray Inspection Methods
For PCBs, x-ray inspection methods provide a great deal of an advantage over normal optical inspection methods. These include:
- Non-Destructive
○ The inspection is carried out using a non-destructive method, which means that there is no risk of damaging the board or its components. - Examines Internal Structure
○ This enables a detailed examination of internal PCBA structures. Hidden flaws, such as voids and cracks that could not be seen externally, can be easily located. Additionally, it is possible to validate the quality of concealed solder joints. - Dimensional Measurements
○ Precise dimensional measurements can be made with X-rays. It includes measuring distances, diameters, and volumes. It is possible to create 2D images and 3D models with details of the internals of a PCBA, with accurate mapping of defects at their true locations. - High Precision
○ The short wavelength of X-rays offers high precision. This allows the determination of extremely fine sub-millimeter defects. The use of X-rays is critical for maintaining high-quality standards because no other method is equally precise. - Software Algorithms and AI
○ Modern automated X-ray inspection methods make liberal use of advanced software algorithms and AI or artificial intelligence. That speeds up the inspection process and makes it more effective. No other inspection method offers such detail and precision of internal defects in PCBs.
Challenges and Limitations of X-Ray Inspection Methods
Although X-ray inspection methods are extremely powerful, they must meet some challenges and have their limitations:
- With electronics trending increasingly towards miniaturization, and boards towards ultra-fine features, X-ray imaging resolution limits are continually being challenged.
- Challenges come from homogeneous materials with low-contrast defects that X-rays find hard to discern.
- Metal shields, connectors, and large BGAs are large enough to block X- rays and do not allow the X-rays to reach the underlying defects.
- Fiber optic, microwave, and Radio Frequency components may need specialized techniques for X-ray inspections.
- Pinpointing vertical defect positions is not possible with 2D X-ray techniques.
- Effective identification of defect signatures and analysis of images requires operator skills.
- Using X-ray equipment requires mandatory safety procedures that add to overheads.
- Widespread deployment may not be possible due to the high up-front cost of X-ray inspection systems.
Conclusion
The benefits of preventing failure with X-ray inspection systems far outweigh the cost for mission-critical aerospace, defense, medical, and automotive applications. PCB manufacturers need to thoroughly understand the principles of X-ray inspection systems to maximally leverage the quality levels of their products. Rush PCB Inc. recommends using X-ray inspection as it is an indispensable process for inspecting the printed circuit board and its assembly.
FAQs
Can we inspect all types of PCBs with X-rays?
Yes. But it is especially useful for inspecting boards with dense components, including those with BGA and other packages where solder joints are below their bodies. They could also be used to inspect multi-layered boards with a complicated internal circuit.
What defects can X-ray inspection uncover?
With X-ray inspection, it is possible to uncover many types of defects like solder joint defects, component placement errors, damaged or broken components, debris from foreign objects, internal cracks, delamination, voids, solder bridges, inadequate solder, and much more.
Which is better, X-ray inspection, or AOI?
While AOI is cheaper, it has severe limitations, especially for highly packed multilayered boards with components like BGAs, CSP, DFN, QFN, etc. AOI uses visible light for inspection and cannot detect defects hidden below the component bodies and the top surface of the board. The higher penetrating power of X-rays allows you to go deeper and look at the internal structure and defects there.
Is X-ray inspection suitable for rework and repair of boards?
Yes. By revealing detailed internal structures, X-ray inspection methods can aid rework and repair of boards.
How to select a PCB X-ray inspection system?
When selecting the type of PCB X-ray inspection system, the manufacturer has to think about capabilities (magnification and resolution) and techniques they support [2D, 3D, CT]. Moreover, they should also look towards the speed and throughput it will give, and also towards the ease with which it can be integrated into the existing processes in the manufacturing configuration.