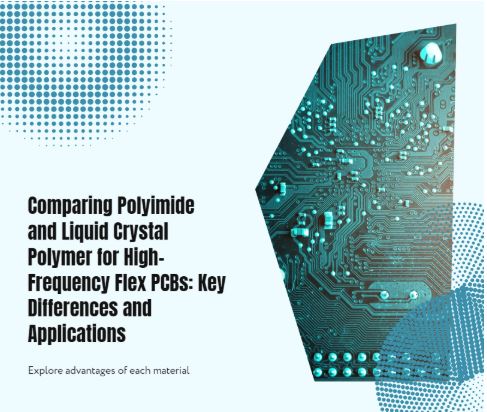
As an emerging dielectric material, LCP or Liquid Crystal Polymer has gained popular attention, especially as an organic packaging material and a high-performance flexible PCB substrate suitable for microwave frequencies. Unlike widely used traditional dielectric materials such as FR-4 and polyimide, LCP substrates come with unique performance and properties. In this article, we, at Rush PCB Inc., compare the characteristics of Polyimide and LCP to illustrate the suitability of these substrate materials for high-frequency applications.
Polyimide PCB Substrates
One of the most widely used substrates, Polyimide films such as Kapton, offer an excellent balance of electrical performance, heat resistance, and flexibility.
The superior characteristics of this popular material allows it to be extensively used in fabricating flexible circuits. Its features make it highly suitable for applications demanding high reliability and endurance under challenging conditions.
Liquid Crystal Polymer PCB Substrates
Manufacturers are now using a better substrate material, LCP, with excellent low dielectric constant and moisture resistance. They often choose LCP for applications prioritizing environmental resilience and those which must have high signal integrity.
Three characteristics, high heat resistance, low dielectric constant, and low moisture absorption make LCP substrates suitable for use in applications exposed to harsh environments. Moreover, its low dissipation factor and low dielectric constant are desirable for high-frequency applications.
Differences Between Polyimide and LCP
Polyimide materials are highly popular, and many manufacturers use it extensively for making flexible PCBs. Hence, although it is readily available, it is more expensive compared to other regular materials. In comparison, LCP, being a more recent introduction, has limited availability. The table below lists some important characteristics of the two materials:
Characteristics | Polyimide | LCP |
Dielectric Constant | 3.4 | 2.9 |
Loss Tangent/Dissipation Factor | 0.002 | 0.0013 |
Insertion loss (dB/mm @ 40 GHz) | 0.18 | 0.11 |
Dielectric Strength (V/mil) | 5300 | >5000 |
Young’s Modulus (kpsi) | 360 | 2700 |
Thermal Expansion (ppm/°C) | 20 | 17 |
Glass Transition Temperature (°C) | 400 | >300 |
Moisture Absorption (%) | 1.7 | 0.04 |
Chemical Resistance | High | High |
Design Considerations | Highly flexible | Less flexible |
Processing Options | Special requirements | Special requirements |
Availability | Readily available | Not available readily |
Cost | High | Higher |
Advantages of Polyimide
For manufacturing flexible circuits, Polyimide is a well-established material. It has several exceptional characteristics like electrical insulation, mechanical strength, and thermal stability, that make it so popular. As it has excellent dielectric properties it is extensively used in high-frequency applications. Moreover, its characteristics are suitable for applications demanding high reliability and endurance under challenging conditions.
Polyimide can withstand extreme temperatures, such as those inside a reflow oven when soldering with lead-free solders. Moreover, it can efficiently operate in temperatures ranging between -200 °C and +300 °C. This makes it ideally suitable for industrial, automotive, and aerospace applications where temperatures fluctuate significantly.
Polyimide materials, with their high mechanical flexibility, can bend and flex repeatedly without damage. Therefore, Polyimide is a strong choice for wearable applications and those requiring continuous movement.
Advantages of LCP
As a more recent material, LCP has already established itself as a contender in specific high-performance applications. Because of its low dielectric constant and excellent moisture resistance, manufacturers typically choose LCP for applications prioritizing environmental resilience and signal integrity.
LCP substrates, with their hydrophobic nature, offer an excellent choice in equipment operating in high humidity, or where moisture could degrade their performance, such as for sensors operating under water or in medical devices. Microwave designs often need low-humidity absorption dielectric substrates, as moisture absorption is a great concern, leading to significant losses in devices like transmission lines, filters, and antennas. The high moisture absorption of Polyimide makes it unsuitable for such use.
The low dielectric constant and low loss tangent of LCP, which practically remain constant over a wide frequency range, ensure minimal signal loss. This makes LCP an attractive option where high frequencies are applicable, such as in microwave and RF circuits.
Disadvantages of LCP
While LCP is flexible, in comparison, Polyimide is even more so. Moreover, Polyimide is more robust than LCP. Therefore, in applications demanding repeated twisting or bending, LCP may be more prone to failure.
Secondly, due to its popularity being not as high as that of Polyimide, availability of LCP raw material is limited, and hence, it is more expensive to manufacture. For this reason, high-end applications tend to use LCP more, where its unique benefits justify the added cost.
How to Select the Right Flexible PCB Substrate
The designer must take into account several factors when choosing the right substrate material. These factors depend on product lifetime, performance requirements, and the application environment. Some key considerations for selecting the right flexible PCB substrate are:
Flexibility
Does the application require the circuit to be static or dynamic? For dynamic circuits, should it handle tight, repeated bending or light, random flexing? LCP substrates have limited flexibility; is this acceptable for the project?
Temperature Range
Will the PCB undergo lead-free soldering (higher temperatures)? What will be the limits and range of the operating and storage temperatures?
Frequency Range
Will the PCB operate at microwave or RF frequencies? Will it require impedance control? Is signal integrity important for the circuit to function? Circuits operating at high frequencies may require substrates with specific dielectric constants.
Environment
Will the application experience high humidity? High-humidity environments may require PCBs with low moisture absorption capability.
Cost
Is LCP substrate necessary for the project? LCP substrates can be expensive, will the project budget allow the additional expense?
Lifetime
How long must the product perform reliably? For better longevity, it may be necessary to use films with higher performance.
Conclusion
Rush PCB Inc. has observed certain distinctive features of microwave characteristics of LCP flex material like transmission line performance and dielectric properties. These include low loss tangent and dielectric constant up to 40 GHz, highly stable dielectric properties even at high humidity situations, and very low insertion loss in comparison to Polyimide materials.