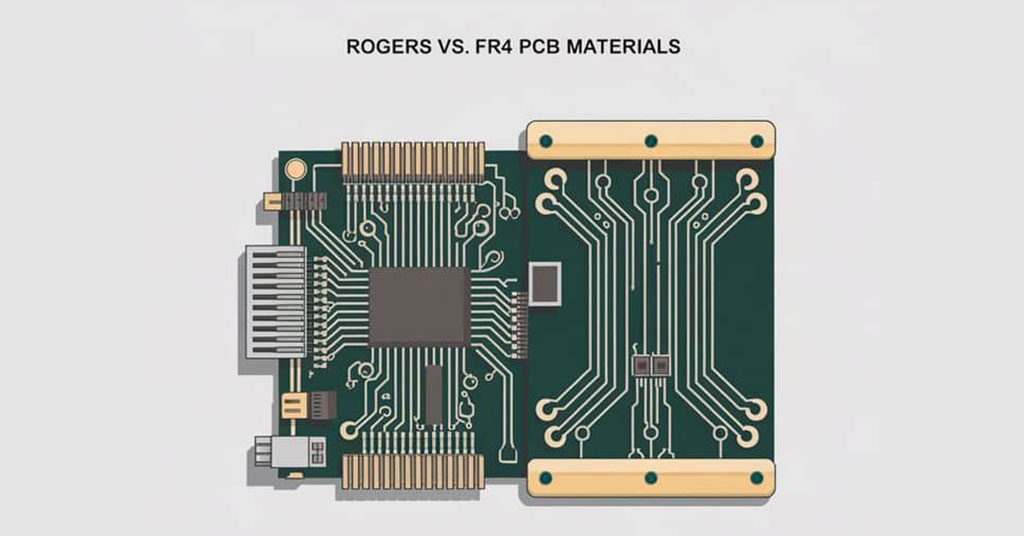
Introduction
PCBs or printed circuit boards must be made from the right materials to deliver the performance expected of them. The proper choice of materials for a PCB not only affects its final quality and cost but also its functionality and performance. Among the many types of materials available for manufacturing PCBs, two are most commonly used. These are FR4 and Rogers. Each of them has its merits and demerits, and its range over which it operates best. At RUSH PCB Inc., we will examine the two materials separately, then make a comparison, and finally, decide the factors based on which you can easily choose the one most suitable for your application.
What is FR4 Material?
FR4 is an acronym for Fire Retardant, Grade 4. It means that the material is not fire-proof, and although it can catch fire, it is self-extinguishing. Moreover, Grade 4 means there are other grades like 1, 2, 3, and 5, with different characteristics:
Material | Loss Tangent | Dielectric Constant Dk | Tg °C | Flame Retardance |
FR1-Basic phenolic resin with paper substrate | 0.040-0.050 | 4.50-6.00 | 105-130 | Fair |
FR2-Cotton Paper Phenolic | 0.030-0.050 | 4.80-5.20 | 130-140 | Good |
FR3-Synthetic Fiber Epoxy | 0.020-0.033 | 4.20-4.80 | 140-170 | Better |
FR4-Woven Glass Epoxy | 0.020-0.027 | 4.30-4.80 | 130-180 | Best |
FR5-High Tg Woven Glass Epoxy | 0.015-0.023 | 3.50-4.80 | >170 | Excellent |
Among the above, the FR4 PCB material is the PCB industry standard, as the woven glass material along with brominated epoxy resin and copper foils gives it the optimal balance of capabilities.
FR4 is electrically stable. It can be made into low-loss laminates that offer excellent heat resistance along with impressive physical strength. Above 90% of all PCBs manufactured use FR4 as the dielectric material.
Advantages of FR4 Material
Compared to other PCB materials, FR4 surpasses them in almost all essential mechanical, electrical, and thermal metrics. This has made the FR4 material a universal choice in the electronics field.
Mechanical Properties
- High flexural strength for enduring mechanical stress
- Resistant to vibration/shock with resilience to fracturing
- Good z-axis compliance
Electrical Properties
- Consistent dielectric constant over a wide frequency spectrum
- Low-loss tangent preserves signal integrity
- Very good insulation resistance at various humidity/temperature combinations
- Suitable for potting and conformal coatings
Thermal Properties
- Glass transition rating varies from 130 to 180 °C
- Can withstand over 260 °C for short term
- Low CTE expansion on Z-axis
Flammability
- Surpasses UL94V-0 3X at 0.75 mm+ thicknesses
- High bromine content causes rapid self-extinguishing when burning
What is Rogers Material?
Rogers PCB materials, made by the Rogers Corporation, are other popular materials for making PCBs. Unlike FR4 materials which are based on glass fabric and epoxy resin, Rogers materials are either ceramic-filled PTFE or hydrocarbon resin systems. With excellent dielectric properties, Rogers PCB materials are eminently suitable for use in high-frequency and microwave equipment. Various types of Rogers materials are available with different characteristics:
Material | Dissipation Factor | Dielectric Constant Dk | Td °C | Flame Retardance |
RO4003C | 0.0021-0.0027 | 3.38 | >280 | V-0, UL 94 |
RO4350B | 0.0031-0.0037 | 3.48 | >280 | V-0, UL 94 |
RO3035 | 0.0015 | 3.5 | 500 | V-0, UL 94 |
RO3010 | 0.0022 | 10.2 | 500 | V-0, UL 94 |
RO3006 | 0.0020 | 6.15 | 500 | V-0, UL 94 |
RO3003 | 0.0010 | 3.00 | 500 | V-0, UL 94 |
Rogers material formulation is available for several applications:
Rogers 4000 series is suitable for power amplifiers, antennas, and RF/microwave circuits.
Rogers 3000 series is suitable for automotive radar and satellite applications.
Rogers 6000 series is suitable for military and aerospace applications.
RT/droid series is suitable for high-power and space-grade applications.
Of the above, RO3003 is most optimized for high-frequency stability requirements. It is commonly used depending on its specific electrical and mechanical characteristics.
Advantages of Rogers Materials
There are several advantages to using Rogers materials for PCBs:
Low Dielectric Loss
Rogers PCB materials, with their low dielectric loss, significantly reduce signal loss, specifically at high frequencies, making it eminently suitable for microwave and RF applications.
Consistent Dielectric Constant
The consistent dielectric constant of Rogers PCB materials allows for consistent impedance control, significantly reducing signal distortion.
Good Thermal Conductivity
Rogers PCB materials have very good thermal conductivity, which helps in effective heat dissipation, thereby preventing overheating.
Low Moisture Absorption
Rogers PCB materials are very reliable in wet environments, owing to their low moisture absorption capability. This makes them well-suited for telecommunications and aerospace applications.
Comparing Rogers PCB Materials and FR4 PCB Materials
The general performance of a printed circuit board is a critical factor. It primarily depends on the materials used to build the PCB stackup. Rogers PCB materials are typically suitable for RF applications and high-reliability systems, such as in military applications. Some material properties that make Rogers PCB materials better than FR4 are:
Properties | FR4 | Rogers |
Dielectric Constant (Dk) | 3.4 to 4.8 | Less than 3 to 10 |
Dielectric Loss / Loss Tangent (Df) | 0.012 to 0.02 | Less than 0.01 |
Dissipation Factor (%) | 0.02 | 0.004 |
Glass Transition Temperature (Tg) (°C) | 130 to 180 | ~ 280 |
Coefficient of Thermal Expansion (CTE)(ppm/°C) | 16 (X-Y), 70 (Z) | 15 (X-Y), 25 (Z) |
Thermal Conductivity (W/m-K) | 0.1 to 0.3 | 0.69 to 1.7 |
Cost | Low | High |
Excellent Dielectric Properties
The dielectric constant, Dk, of Rogers materials remains stable over a wide range of frequencies. Not only is this crucial for high frequency circuits in maintaining signal integrity, it also ensures that the impedance remains constant, helping to maintain signal speed, and reducing the risk of distortion and signal loss.
In addition, Rogers materials also exhibit very low dielectric loss. This means the material can effectively transmit signals with very little absorption. This is very important for applications like RF and microwaves, where signal strength and clarity are critically important.
Rogers materials exhibit significantly lower dissipation factors as compared to FR4 materials. This means Rogers materials contribute substantially to lower signal loss, thereby improving the signal integrity.
Thermal Management Capabilities
Circuits handling high-frequencies often generate substantial amounts of heat. If not removed promptly, the heat can raise temperatures, affecting the performance and longevity of the board. As Rogers laminates have high thermal conductivity, they can effectively dissipate heat much better than conventional materials.
In addition, Rogers materials also exhibit very low CTE or Coefficient of Thermal Expansion. This property allows the PCBs to maintain their dimensions despite wide temperature fluctuations. While high thermal conductivity helps to maintain operational stability of the circuit, low CTE offers high stability for maintaining the PCB’s structural integrity even when the temperature is varying over a large scale.
The Tg or glass transition temperature for Rogers material is substantially higher than that of FR4 PCBs. This is of great advantage when using lead-free materials for soldering, as most lead-free solders have a high melting point.
Superior Mechanical Properties
Rogers materials exhibit excellent resistance and durability to mechanical stress. This makes them suitable for applications requiring reliable and robust performance. The rigidity of the PCB material allows it to retain its shape and functionality even when the operating conditions are challenging.
Furthermore, with Rogers materials being compatible with various fabrication processes like advanced laser drilling and sequential lamination, the versatility of the material allows manufacturing of complex and high-density circuits with exceptional efficiency and precision.
Diverse Applications
The telecommunications sector uses Rogers materials extensively for producing antennas, base station equipment, and satellite communication systems. Defense and aerospace industries use them for avionics, radar systems, and other devices for critical communication systems.
In the automotive industry, Rogers material is used in high-frequency applications like ADAS or advanced driver assistance systems. The medical industry, where reliability and precision are crucial, depends on Rogers materials for imaging systems and diagnostic equipment.
Which is Right for Your Application — Rogers or FR4?
You may have to consider the following criteria when choosing the right PCB material for your application:
Application Criteria | FR4 | Rogers |
Signal Frequency | <500 MHz | >500 MHz |
Soldering Temperature | <150 °C | >200 °C |
Operating Temperature | <80 °C | >80 °C |
Thermal Cycling | low | High |
Cost to Performance Ratio | High | Low |
Conclusion
At RUSH PCB Inc., we consider the FR4 material as versatile and ideal for standard electronic applications. On the other hand, we consider the Rogers material better suited for high-performance and high-frequency applications, as it offers better thermal stability and superior signal integrity. Most often, the choice between the two depends on the specific performance required and the budgetary requirements of the project.