Although the electronic industry uses a Bill of Materials (BOM) to indicate a list of ingredients a product uses, the concept of a comprehensive BOM is still elusive to most people. To create a proper understanding, Rush PCB is hereby providing a guide to generating and qualifying a proper BOM. Typically, a BOM is a list of raw materials, components, assemblies and subassemblies, and other crucial items a manufacturer will need for building up a product.
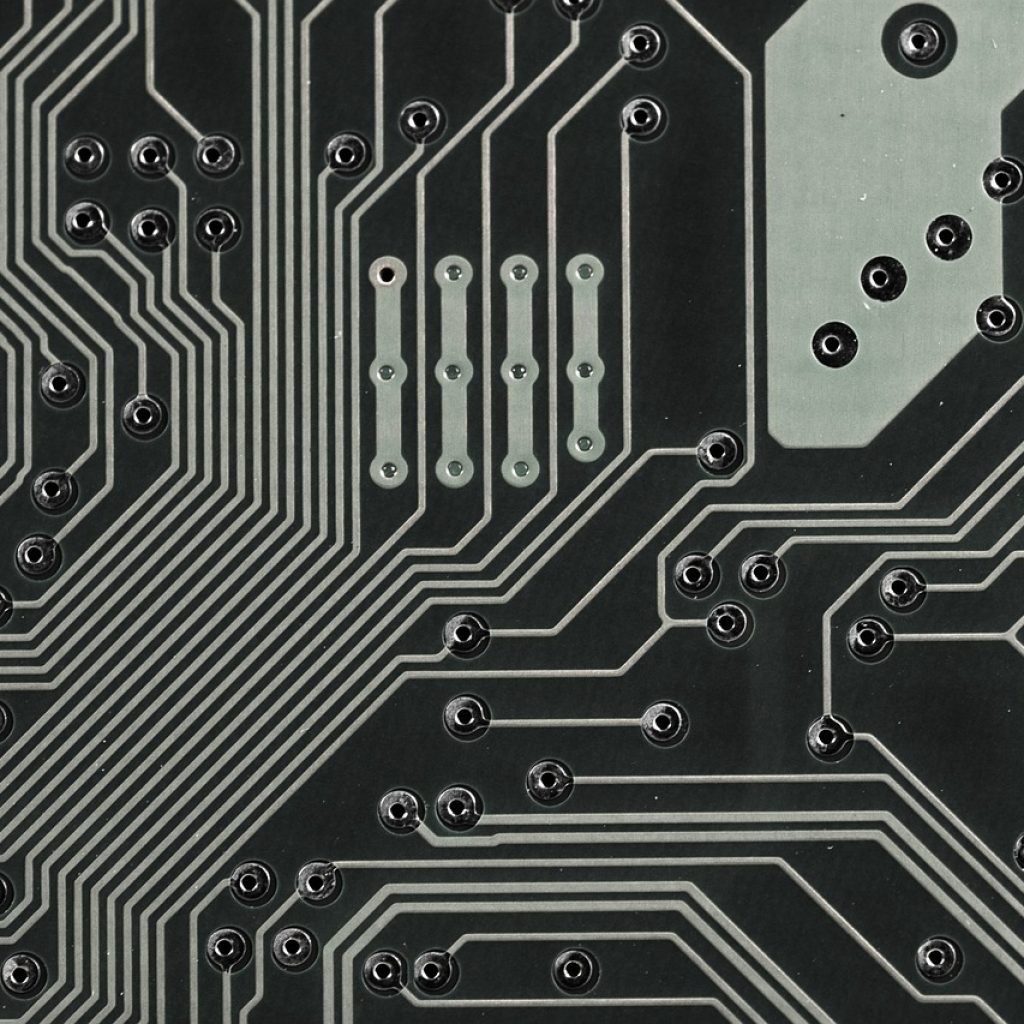
Though a manufacturer has to depend on the information within the BOM to build a product, its content must not only be sufficiently detailed, but also highly accurate. OEMs use BOMs to instruct PCB manufacturers and assemblers their requirements when they order circuit boards and assemblies. In turn, assemblers use the customers’ BOMs to build the board to their specification.
At Rush PCB, we provide numerous PCB assembly services, and the BOM plays a crucial role.
Creating a Bill of Materials-PCB
No doubt, creating a detailed Bill of Materials is time-consuming, developers usually relegate this task to the end. However, the BOM is an important document, as it makes the PCB production process more efficient. For complex designs, a BOM also acts as a reference document, preventing costly mistakes. Therefore, prior to BOM creation, the developer should have clarity on the type of product they are undertaking.
As developers enter the design phase, they have more information on the components that will go into their product. As they proceed further, they collect additional information they can add to their initial BOM. In fact, the BOM is not complete until the developers have completed their design. For a PCB, this amounts to the generation of a Gerber file that the manufacturer can successfully use to fabricate the PCB.
Most product developments undergo at least one or more iterations, so periodic changes to a BOM is perfectly natural. Additionally, in the course of product development and later, several people will be using the BOM in different ways. For instance, purchasing orders for some material in the BOM may have to be placed early on, as they require long lead-times, while some items may require special permissions and governmental clearances that take time. Therefore, it is essential to set up a system for editing and managing the information in a BOM.
Surely, multiple departments will use the information in the BOM in their own way, it is essential to decide the manner of dissemination of the document. For instance, while the purchasing department will be using the information to place orders to component manufacturers, the engineering department will use the same information to set up their assembly and testing machines.
Read About: DIFFERENCE BETWEEN PCB PROTOTYPING & STANDARD PRODUCTION
BOM Structure – PCB
The structure of the BOM depends to a large extent on the strategies the OEM follows. Some prefer to make multiple BOMs to support the different levels and subassemblies a product will have, while others may simply have a single BOM divided into several levels. Whatever the structure, Rush PCB recommends BOMs to have data arranged efficiently and unambiguously.
Developers mostly use PCB CAD software packages to create their schematics and PCB layout. While doing this, they have to input the details of electronic components that will go into the PCB. Most PCB CAD software packages are capable of using this information from the developers to generate the primary BOM, listing the part names, their individual quantity, and their positional identities on the PCB. Usually, this primary document is in the form of a spreadsheet, and it is possible to add information to it later by creating additional rows and columns as necessary.
Complex designs require BOMs that cater to several requirements. For instance, consumer electronic industries may manufacture several products that use a common PCB, but different onboard components. Generally, it is easier to create a database of all the components they use, and tag their usage with the product identity, positional identity, and individual quantity in specific products. Generating a BOM is then a simple affair of filtering the contents of the database with the name of the product.
Read About: AVOIDING COMMON PCB FAILURE MODES
Information in a BOM – PCB
Although the detailed information in a BOM depends on the complexity of the product, the names of the parts and their individual quantities required, form a necessary basic information. It is usual to add other optional information, such as the name of the preferred supplier and alternate sources of supply. Making the BOM as detailed as possible and complete helps reduce bottlenecks at many stages. Rush PCB suggests developers include at least the following information in their BOMs:
- Part Number
- Reference Designator
- Manufacturer’s Name
- Description of Part
- Quantity
- Procurement Type—Custom made or Purchased Off-the-Shelf
- Source
- Alternate Parts
- Package Type
- Footprint
- Placement Method—SMD or Through-hole
- Placement Layer—Top or Bottom
Apart from the above, developers must also place comments and notes for the benefit of component purchasers, handlers, assemblers, and others as they see fit. For instance, developers may place special notes or markers against parts susceptible to ESD failure.
At Rush PCB, we offer a full range of PCB services, with an overall focus of quality. Company’s full turnkey services include procurement, fabrication, assembly, and testing. Our one-stop approach makes it easy for our customers to get their project completed on time.
Our online quoting is instant, and facilitates reordering. Visit our website today, and submit your BOM and Gerber files to get an instant quote.