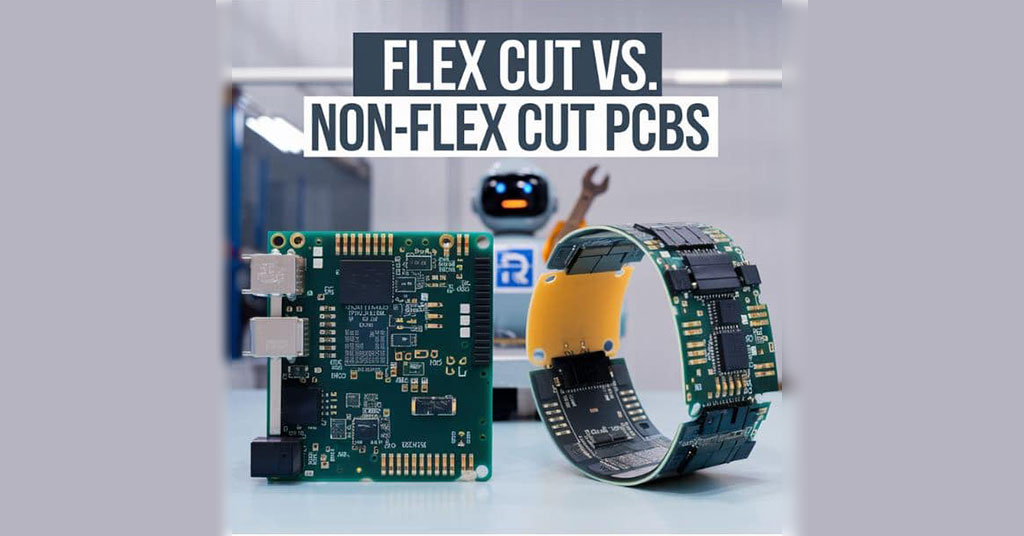
Introduction
Many modern electronic appliances nowadays use flexible circuit boards as these offer several advantages over the regular rigid variety. High-precision lasers or other mechanical tools that perform precise cutting operations on flexible circuit board materials are referred to as flex cuts. A high-precision cutting technology utilizes precision lasers or mechanical tools to create complex shapes or small sizes of boards through control from advanced computerized systems.
In contrast, non-flex cut PCBs refer mainly to circuit boards made of rigid (non-flex) materials cut with standard cutting technologies. As the material of these boards is often hard, the cutting technology uses diamond saw blades or high-speed rotating milling cutters.
Some equipment uses a combination of flex and rigid PCBs. Typically, this is an integration of the two types, wherein the board has some rigid parts and some flexible sections. Two or more rigid parts may also be interconnected with flexible sections. This offers many advantages over independent flex or rigid boards. The flex part of the PCB often has slits or cuts made in certain areas, allowing it to bend or flex without damage. The cuts and slits require a precision laser or mechanical tools to create them. Rush PCB Inc. makes all types of boards and provides key differences and applications for flex cut and non-flex cut PCBs in modern electronics.
Why Flex Cut Technology is Necessary?
The USP of a flex PCB is its capability to bend or flex continuously without damage. To achieve this, the flex PCB, often a part in-between two rigid sections, may require a special shape, cut, or slit to facilitate easy bending. A very careful design goes into generating the shape, cut, or slit necessary to allow the PCB to withstand mechanical stresses when bending, without causing damage to the copper traces on it.
Typically, the flex part of the PCB is made of flexible materials like Polyimide. This allows it to repeatedly bend without compromising the integrity of the board. The combination structure of flexible and rigid parts within flex cut PCBs works exceptionally well when boards require compact folding or bending or shaping to fit into unstandardized enclosures.
Advantages of Flex Cut Technology
Flex cutting technology offers many advantages, most of them common to those of flex boards:
Space Saving — Space-saving benefits emerge from flex cut PCBs because they can easily fit into restricted areas. Flexible and rigid fusion areas produce optimal results that fit well into compact products including wearables along with smartphones and portable electronic devices.
Weight Reduction — Being significantly lighter than regular rigid PCBs, flex cut PCBs are more suitable for applications where reduction of weight is critical to their operation.
Improved Durability — As flex cut PCBs can bend and flex many times without damage, they are significantly more durable as compared to their rigid counterparts. Due to their flexibility polymers can withstand mechanical failure caused by constant vibration or movement in objects such as foldable phones and cameras along with industrial machinery.
Better Reliability — The absence of cables and connectors in board interconnection makes flex cut PCBs reduce the number of potential device failure points. The improvement in reliability is also due to the simplified assembly processes and at the same time, it reduces costs.
Versatile Applications — Flex cut PCBs open up a very wide range of applications. Many devices use a combination of flex and rigid PCBs. The applications extend to automotive sensors together with medical implants, military equipment, and aerospace technologies. Flex cut PCBs can also withstand harsh environments, which makes them eminently suitable for several industrial and outdoor applications.
Cost-Effective — In comparison with regular rigid boards, flex cut PCBs are more expensive. However, the increase is offset in the long run because of their improved durability, better reliability, and their ability to replace connectors and wiring. Manufacturers use these spacious components to construct tiny enclosures that reduce production expenses and materials requirements.
Comparison Flex Cut Vs. Non-Flex Cut PCBs | ||
Parameter | Flex Cut PCB | Non-Flex Cut PCB |
Material | PI / PET / PEEK | FR4 / CEM-1 / CEM-3 |
Flexibility | Can bend & flex | Rigid, non-flexible |
Accuracy | Highly accurate | Medium accuracy |
Safety | Highly safe | Highly safe |
Efficiency | Laser cutting is efficient | Mechanical cutting is less efficient |
Stability | Highly stable | Highly stable |
Applications | Flexible and miniature electronic devices | Large and power electronic devices |
Applications in Modern Electronics
Flex Cut PCBs
Various industries, mainly those requiring durability, flexibility, and compactness, use flex cut PCBs. Some common applications include:
Automotive Industry
The automotive sector operates numerous electronic gadgets that require tolerance to vehicle interior conditions. Not only is there a severe lack of space inside a vehicle, but the temperatures are often high, and there is severe vibration. The flex cut PCB can withstand all the above and is, therefore, an excellent choice for automotive control and sensor systems.
Military and Aerospace
The military and aerospace industry often requires lightweight but robust equipment that can withstand harsh environments such as those in the arid desert, humid seas, and intense space radiation. Flex cut PCBs are eminently suitable and capable of withstanding such harsh environments.
Medical Devices
The best application for flex cut PCBs is implantable devices together with minimally invasive medical equipment because these components demonstrate flexibility combined with lightweight and biocompatibility.
Wearable Devices
Smart watches and fitness trackers benefit greatly from using flex cut PCBs because they need to fit human body curvature.
Foldable Electronics
Due to escalating market demand for foldable products, manufacturers utilize flex cut PCBs to enable their hardware devices to fold and bend without suffering any damage.
Non-Flex Cut PCBs
Various industries, mainly those requiring rigidity, durability, and power handling, use non-flex cut PCBs. Some common applications include:
Consumer Electronic Devices
Large consumer electronic devices like audio amplifiers, television sets, desktop personal computers, HVAC units, refrigerators, and more, use non-flex cut PCBs. These devices typically have plenty of space within and must dissipate heat, which makes it more suitable for their use of non-flex cut PCBs.
Power Converters and Inverters
Power converters and inverters operating at high power levels require processing large currents and voltage levels. Often, this calls for thicker copper traces and higher spacing between conductors. Non-flex cut PCBs are eminently suitable for such applications.
Military Applications
Military radar and missile technology need stable operation under all conditions for reliable performance. Non-flex cut PCBs meet these requirements suitably.
Conclusion
Rush PCB Inc. reports that existing electronics need flex cut and non-flex cut technologies because they serve different purposes and distinct specifications for specific applications. Both technologies play independent but important roles in the electronic manufacturing industry. As the market demand changes and manufacturers update electronic products, the demand for these two technologies will continue to develop. Innovations will inject new momentum into the future of these useful technologies.