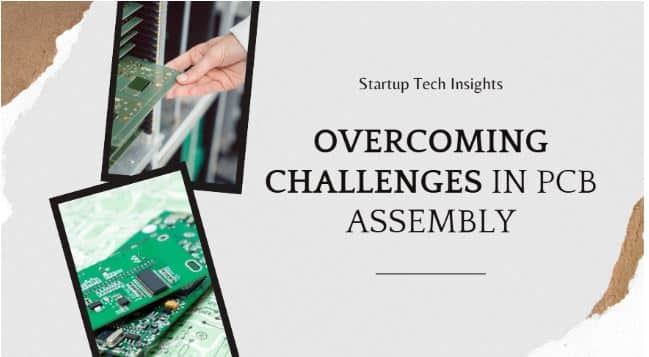
Introduction
PCBs or Printed Circuit Boards are essential for almost all electronic equipment. Most mass-produced electronic equipment commonly use high-volume PCB assembly. However, startups typically manufacture products in lower quantities, for which they need PCB assemblies in low volumes. Companies that manufacture smaller quantities of PCBs experience different manufacturing difficulties compared to enterprises that work at high volume levels. Rush PCB Inc., a renowned manufacturer of all types and volumes of PCBs and PCB assemblies, discusses these challenges and offers possible solutions. But first, we must distinguish between low-volumes and high-volumes in the context of PCB assemblies.
What is Low-Volume PCB Assembly?
Although it is difficult to quantify the exact volumes of PCB assembly that qualify as low-, mid-, or high-volumes, the industry uses some thumb rules. The following table offers these rules. However, preferably do not consider these rules as strict, but treat them only as a guideline.
TYPICAL VOLUMES OF PCB ASSEMBLY | |
Prototyping | 1 – 10 Boards |
Pre-Production | 10 – 50 Boards |
New Product Introduction (NPI) | 50 – 100 Boards |
Short Run Production / Low Volumes | 100 – 1000 Boards |
Medium Volumes | 1000 – 10,000 Boards |
High Volumes | 10,000+ Boards |
Note that before starting any substantial quantity of production, a manufacturer starts cautiously with low quantities, to allow testing and verifying the product design before embarking on a full high-volume production run. Short-run productions are also suitable for those who do not intend to manufacture many thousands of PCB assemblies.
Customized hands-on assembly is possible only at low volumes, together with close customer collaboration. This flexibility is most suitable for startups and those introducing new products, small-scope use cases, short life-cycle projects, and specialized industrialized equipment manufacturers.
Any Advantages of Low-Volume PCB Assembly?
Why do startups go for low-volume PCB assembly? That’s because low-volume PCB assembly offers substantial benefits:
- Faster Turnaround — The manufacturing pace of PCBs at low volume levels enables quick turnaround capability. There are several reasons for this:
- Lower procurement times — A smaller number of components can usually be procured from multiple ready suppliers. However, large consignments require longer lead times.
- Lower handling times — With lower inventory, incoming inspection times are lower, also requiring lower resources.
- Low storage space requirements — Systems with fewer components need lower storage space while cataloging needs remain minimal. Also, tracking and retrieval operations become faster and easier because of the smaller number of parts.
- Lower assembly times — Even when the assembly time per board is the same, the total production run finishes in a shorter time for low volumes.
- Lower inspection times — Compared to the total inspection time for high-volume production, inspection time for low volumes can be comparatively smaller.
- Design Flexibility — As it is easier to evaluate a small quantity of PCB assembly, any design changes and modifications can be done faster. With small quantities involved, making changes in the BOM or Bill of Materials and PCB layout becomes simpler and easier.
- Lower Costs — The elevated scale of manufacturing necessitates increased investment in all aspects including purchasing, storage infrastructure, equipment procurement, and facility infrastructure as well as testing systems. Low-volume assembly can do with lower startup costs.
- Scale Economies — Manufacturers compensate for higher production expenses related to small-quantity production by increasing their per-unit cost. The production levels that scale economies serve best match those of large volumes.
- Lower Risk — A complete evaluation of limited production runs helps decrease risks because potential problems can be identified and fixed before advancing to larger production volumes.
- Customization — The process of low-volume PCB assembly enables manufacturers to apply product-specific customization requirements during product refinements. The standard industrial approach involves highly automated systems in high-volume production.
- Quality Checks — As the overall number of boards is lower in low-volume assembly, each of them can be inspected directly, as against selective sampling for mass production.
Challenges in Low-Volume PCB Assembly
As listed above, low-volume PCB assembly is common among many startups and product development teams. It is especially helpful during their prototyping and small-scale production phases. Compared to high-volume production the major benefit of low-volume assembly includes cost savings combined with flexible manufacturing capabilities. However, it also faces many challenges, for which we have suggested solutions to help startups improve their quality and efficiency.
Higher Per-Unit Costs
The production of PCBs in lower volumes results in increased costs for each unit. This is because the smaller numbers can drive only a limited bargaining power during component procurement. The decreased manufacturing effectiveness resulting from these interruptions leads small businesses and startups to experience budgetary pressure.
Solution for Higher Per-Unit Costs
-
Optimize the Design
It is possible to offset the higher per-unit costs by optimizing the design at the design stage itself. That means, reducing unnecessary features to minimize the BOM, and optimizing the PCB layout. The design process optimization along with standardized parts selection creates opportunities to decrease manufacturing expenses and procurement costs.
-
Choosing the Right Manufacturer
The ability to perform low-volume assembly exists only in selected manufacturing companies. Selecting the right manufacturer who offers competitive pricing by specializing in small batch production can be a useful option. Establishing long-term ties between startups and manufacturers brings both enhanced services and lowered pricing as an outcome.
-
Shared Manufacturing
Some manufacturers share their services, where they combine the orders of several customers in a single production run. This helps to lower the cost per customer.
Components Sourcing Difficulties
As the number of components in low-volume production runs is small, sourcing is often a challenge. Manufacturers might face difficulties obtaining specific components when they are available only in large quantities, and suppliers refuse orders that are too small. The cost of components may also increase significantly because of their smaller numbers.
Solution for Component Sourcing Difficulties
-
Plan Ahead
Advanced planning along with component sourcing provides a defense against supply chain interferences that may occur during production execution.
-
Search for Suppliers Who Handle Small Batches
Prepare and evaluate a list of suppliers who cater to orders in small batches. Some platforms distribute electronic components suitable for low-volume production.
-
Use Alternate Components
Search for and list alternate components during the design phase. The selection should be made based on convenient sourcing capabilities and price stability. Choosing components that are widely available instead of rare or customized parts which may be challenging to obtain during maintenance and repairs is advisable.
Longer Lead Times
Low-volume production requires both customization work and manual labor, thus leading to extended lead times. The lead time depends directly on the time-consuming and complex processes.
Solution for Longer Lead Times
-
Time Planning
Preparing a clear and detailed timeline helps when discussing with the manufacturer. This also allows for more accurate control over times involved in the assembly and production phases.
-
Early Start
Starting the assembly and production processes right after the design phase allows more time for addressing potential issues.
-
Quick Turnaround during Manufacturing
Choose suppliers who maintain adaptable production schedules that enable quick manufacturing times. Choose manufacturers who can manage small production quantities together with fast delivery services.
Quality Control
Good quality control implementation presents additional difficulties during low-volume production operations. This is mainly because of the inability to ensure the same level of stringent testing as is possible in larger production runs.
Solution for implementing Quality Control
-
Stricter QC Processes
It is necessary to implement stricter QC processes even for smaller production runs. The system must contain processes that encompass design reviews in addition to incoming material inspection and in-process quality checking, as well as final product testing.
-
Automated Testing Tools
Automated testing tools can ensure consistency while reducing human error. Use these tools for checking soldering quality, functionality, and other quality assessments.
-
Validation
The testing phase happens before production runs to validate that the PCB design performs as intended. This reduces any rework requirements later.
Technical and Design Changes
Market conditions together with customer needs can compel producers to make technical and design changes in their low-volume manufacturing operations repeatedly. Challenging situations emerge during production since they affect production schedules as well as affect product quality and increase both expenses and timescales.
Solutions for Technical and Design Changes
-
Keep Production and Design Processes Flexible
Find suppliers who show readiness to modify their designs promptly. Work closely with such low-volume manufacturers, who can adjust flexibly during production.
-
Effective Communication
A reliable system for rapid communication must connect all teams including design and engineering with manufacturing to effectively handle changes from both design and production periods.
- Version Control
Every design modification must be recorded and tracked to stop previous errors from reoccurring. Design and manufacturing would benefit from a version control system implementation.
Soldering Issues Post Assembly
Manual assembly together with hand soldering commonly occurs in the prototyping and pre-production phases because production quantities remain limited. Product reliability and operational functionality might decline because of these issues.
Solution to Soldering Issues Post Assembly
-
Use Experienced Soldering Personnel
For manual assembly and hand soldering, preferably ensure the assembly team has considerable expertise to maintain quality. Choose personnel with adequate skill in handling small-scale, high-precision soldering.
-
Use Automated Equipment
Automated soldering systems such as selective soldering machines together with reflow soldering systems significantly reduce low-volume soldering problems. The investment of extra expense results in superior soldering consistency and minimizes the occurrence of defects during soldering operations.
Conclusion
The PCB assembly recommendation from Rush PCB Inc. involves performing low-volume production to ensure electronic design accuracy before advancing to full-scale manufacturing operations. Although this requires a higher cost and effort per board, the smaller scale of builds reduces the risk and provides greater flexibility during product development.
All the advice and solutions presented in this article provide a framework for startups to maximize the benefits of limited-volume production before advancing to full-scale manufacturing. The article provides adequate guidelines to successfully plan a low-volume PCB assembly project.