The surface tension of liquidus solder exerts a considerable pulling force on a component during reflow. This is why, once upon a time, small components could be relied on to self-align on SMT pads during reflow. They still can, of course, providing that all things are equal, such as pad dimensions all around. But if they’re not, you can expect problems.
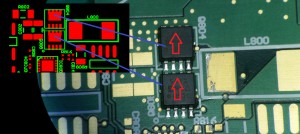
Figure 1. Two SMDs have misaligned during reflow due to uneven pad sizes and disproportionate solder liquidus surface tension.
In this case, two components had shifted away from their center location on the PCB footprint during reflow (Figure 1). This was due to the fact that a large SMT pad on one side of the components, see photo, was exerting a stronger pulling force on the component than the ordinary-size pads on the opposite side. More surface area means more pulling force, and consequently component misalignment. It doesn’t matter that the placement machine put the part in the right location beforehand.
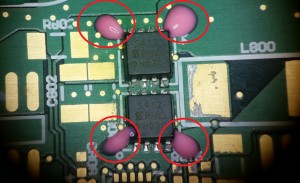
Figure 2. Temporary solder mask glue applied to two corners of each component prior to reflow keeps them in place.
Read About: Misfits
Mechanical fixturing simply wasn’t a practical solution. Instead, two dots of temporary solder mask glue were applied to the corners on one side of each component, prior to reflow, to hold it in place. The glue acts as a temporary adhesive and prevents the parts from moving during reflow because it is stronger than the pull of the liquidus solder. After reflow, the glue is easily removed, and the SMDs are perfectly centered. Problem solved!
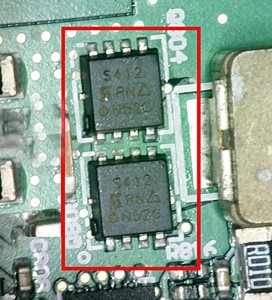
Figure 3. Post-reflow, the adhesive is easily removed, and the SMDs are perfectly positioned as they should.
By Roy
Are You Looking for quickturn prototype PCB manufacturing & assembly of high quality? RUSHPCB is one-stop shop for design, fabrication & assembly of PCBs. www.rushpcb.com Call: 1 408 496 6013 Email: [email protected]