Rush PCB expects a huge impact to the electronic industry from the Implementation of 5G in electronic devices, especially as the new technology offers very high data rates, leading to the expectations of a multi-fold jump in data traffic. However, handling this kind of quality and scale will call for an equally innovative manufacturing requirement. The industry is expecting the innovations to include not only entertainment applications, but also mobile phone connectivity, industrial applications, transportation, and most importantly, the Printed Circuit Board (PCB) manufacturing industry.
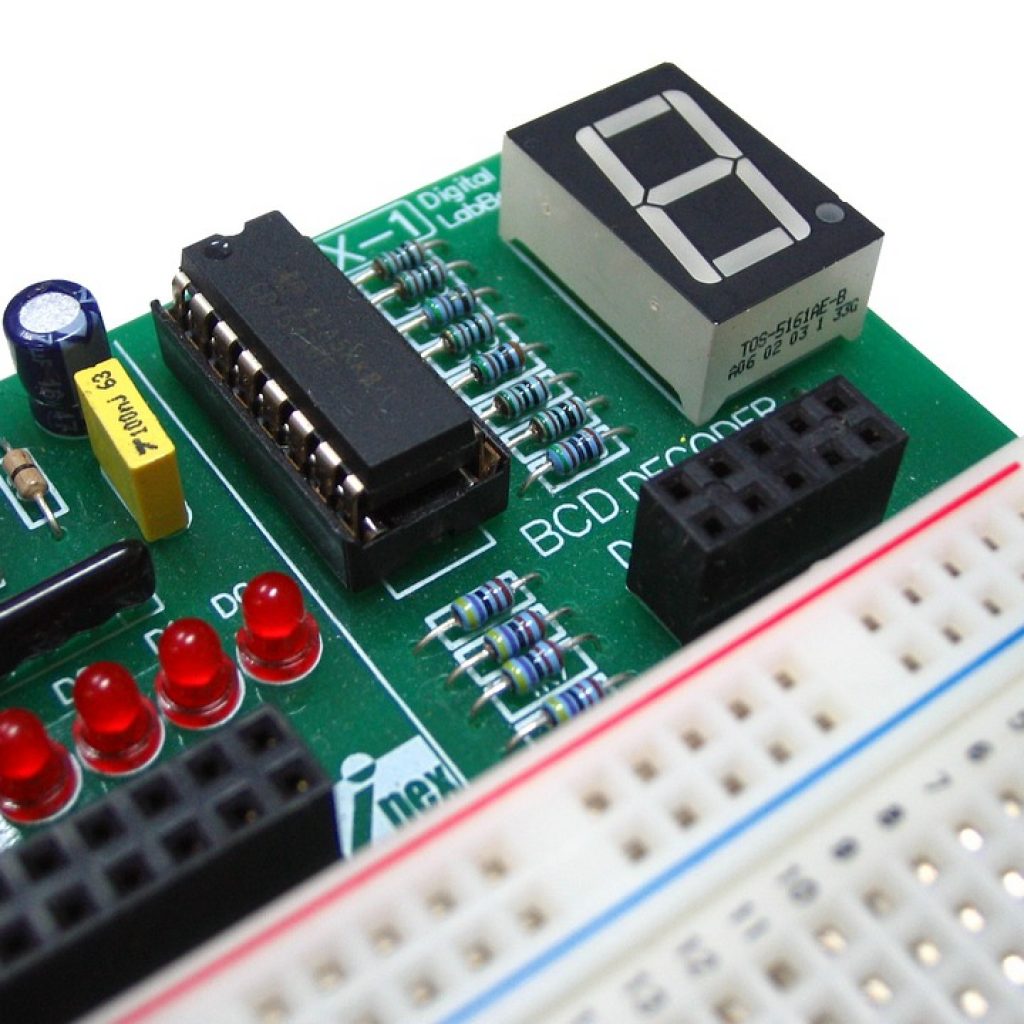
For instance, the high-speed 5G technology requires progressively smaller designs and therefore, thin PCB traces for high-density interconnects. It can easily lead to signal performance deterioration if the manufacturer does not handle the PCB properly, consequently leading to delays in signal transmission, and thereby ultimately impacting data flow. While manufacturers must ensure proper execution of designs for preventing the occurrence of such issues, Rush PCB recommends the use of modified semi-additive processes (mSAP) when manufacturing PCBs for 5G technology, along with Automated Optical Inspection (AOI) tools for inspecting PCBs.
The Conventional Approach
PCB manufacturers use a subtractive process for fabricating conventional boards. They use a chemical treatment for etching and removing the unwanted copper from the foil on the PCB, leaving the required pads and traces. However, along with vertically removing the copper for creating pads and traces, the etching process also dissolves copper in the horizontal direction, along and under the walls of the pads and traces.
Rather than forming traces with rectangular cross-sections, the etching process creates traces with trapezoidal sections. It is difficult to control a chemical process precisely, and the conventional etching process creates non-uniform traces, leading to higher signal loss.
The mSAP Process
In comparison, the mSAP process allows the formation of traces with straight vertical lines and rectangular cross-sections, resulting in uniform cross-section. Impedance in such regularly formed traces is more predictable and controllable, leading to a maximization of circuit density, and far lower signal losses.
Automated Optical Inspection (AOI) Tools
Whatever the type of PCB, defects during the manufacturing and assembly process need detection and correction. Among several inspection methods, manufacturers have found the use of AOI tools to be optimum for locating various defects. So far, they have found AOI tools to be the most suitable for inspecting 5G capable boards. For instance, by measuring the top and bottom traces on a PCB, an AOI system can inspect potential defects. This justifies the additional capacity of an AOI system for producing quality boards.
Rush PCB suggests the use of 2D metrology technology for 5G boards to allow higher impedance control and high sampling rates for high throughput. Further, with the integration of advanced AOI systems, PCB manufacturers can combine different processes on a single platform, thereby increasing the efficiency by saving both labor and time.
Integrated advanced AOI systems have an advantage over conventional inspection tools. Manual inspection usually leads to halting the production during the process of inspection, leading to waste of time. Moreover, manual inspection involves an assortment of tools that occupy precious floor space.
Another aspect of advanced AOI systems is the workflow can include the verification process as well. This again precludes the need for a standalone system to figure out PCB defects. This is an important advantage considering the resource requirements of a verification process may exceed that of an inspection process by a figure of three.
As 5G boards require increased verification, the use of automated AOI systems helps manufacturers free up a lot of resources in the form of floor space or manpower, leading to a significant decrease in costs. Advanced AOI systems make use of artificial intelligence to ensure sifting out false alarms. This allows the operator to focus not only on defects that they can resolve, but also to use sampling to save the time and effort of moving every panel to the verification station. Usually, such advanced systems use a single centralized remote multi image verification station that precludes the need to verify each panel, preventing the risk of panel damage.
Advanced AOI systems also have the advantage of data aggregation and analysis. PCB manufacturers can easily draw relevant insights from the aggregated data, leading to quick decision-making. Such integrated AOI workflows also helps to easily trace PCBs for isolating defective ones. It also makes it easy to withdraw any defective PCB from among those already deployed in devices.
Smartphone PCBs for 5G
Although smartphone manufacturers are constantly under pressure to bring out sleek, compact devices for their customers, they need to differentiate their products in a competitive and crowded market. Within a smartphone, every millimeter of available space is a gold mine for unlocking significant value.
Special PCB manufacturers have been able to relieve some pressure of the form-factor-driven design of smartphone manufacturers by offering them flexible high-density interconnect (HDI) PCBs. Compared to conventional PCBs, HDI PCBs allow more functions per unit area. With very fine lines, thinner materials, and laser-drilled vias, HDI boards are playing a crucial role in miniaturizing the embedded systems of smartphones. However, the HDI system seems to have reached its limit with the 4G LTE technology and needs to evolve to a newer level as the next generation of phones moves towards 5G.
Smartphones working with 5G will be using RF front-ends of increasing complexity, which will widen the RF content footprint considerably within the 5G smartphone. They will also require Massive-MIMO antenna configurations to match the RF systems. With the increased processing power necessary to support the staggering volumes of 5G data, phones will most certainly require larger batteries and geometries. With the increased input output demands, available space for HDI PCBs within a 5G smartphone will shrink significantly.
Additionally, 5G technology makes use of higher frequencies that require far stricter control of impedance than that for 4G LTE. Unless PCB manufacturers form them with extreme precision, HDI PCBs with thinner traces can increase the risk of signal degradation along with lapses of data integrity as discussed above.
The increased frequency and power handling in 5G technology will also require better thermal management of PCB products. Use of high power along with high power density in smartphones will make thermal management a very important factor for smartphone reliability.
Therefore, PCBs for 5G technology will require special heat dissipation structure, such as new high thermal conductivity materials. While traditional PCBs do not harbor such special structures, PCBs for 5G may require much higher precision than conventional PCBs do.
The mSAP Process for Smartphone PCBs
Rush PCB recommends the use of mSAP processes for overcoming the challenges in 5G PCBs. Presently, production of IC substrates makes use of mSAP processes, and the HDI PCB manufacturing industry is in the process of adopting the same technology.
While conventional HDI technology has already achieved line/space requirements of 30/30, and manufacturers expect to decrease that further to 20/20, mSAP can help them achieve these targets easily. This will enable not only unprecedented device density achievements in 5G smartphones, the superior conductor geometries generated by mSAP will offer exacting impedance control for 5G operation at high frequencies.
As compared to the conventional subtractive process for PCBs, the mSAP process is essentially its opposite. The subtractive process uses etch resist to coat the copper layer, photo-lithography to image the areas where the copper needs retaining, and chemical etching to remove the non-imaged copper.
Although a well-established process, the drawback of the subtractive process is the etching process leaves the copper traces with a non-uniform trapezoidal cross-section. This not only compromises the circuit density with wider than intended lines, but also the wedge-shaped traces introduce impedance anomalies at high frequencies.
In contrast, the mSAP process begins with a thin copper layer on the laminate, and a resist coating on the copper to define the areas where the fabricator does not want pads and lines. By plating on to the areas where the resist is not present, the process builds up the thickness of copper traces, featuring the additive nature of the mSAP process. In the next step, the fabricator etches away the thin copper layer between the conductors,
While the conventional subtractive process defines the trace geometries with the help of chemical etching, the mSAP process does this in a far more precise manner using photo-lithography and electroplating. The resulting rectangular cross-section of the traces with straight vertical sides that the mSAP process creates enables lower signal losses due to accurate impedance control. Furthermore, the precise rectangular shape of the traces is more effective in maximizing circuit density.
Advanced HDI Manufacturing Technique — mSAP, AOI, & AOS
Although mSAP technology helps PCB manufacturers produce advanced HDI PCBs for 5G smartphones, Rush PCB suggests implementing mSAP in a manner that maximizes production yield and throughput while minimizing costs for ensuring it offers adequate returns on investment. This is a matter of concern, especially since high volume production of IC substrates can absorb the higher cost of mSAP comfortably. In contrast, the volume scales of smartphone PCB production are far lower, hence the concern for production efficiency and cost.
Also Read: EFFECTIVE PCB MANUFACTURING PROCESS
mSAP
While transitioning from 4G LTE to 5G, PCB manufacturers are investing increasingly in advanced manufacturing tools and techniques suitable for mass production with mSAP. They recognize that precisely formed lines are critically essential for creating HDI PCBs with higher densities.
Rush PCB advises the adoption of advanced direct imaging (DI) systems for achieving line widths of 10 microns with spacing of 15 microns. Such precise uniformity requires high registration accuracy of 7.5 microns, and may also require advanced localized registration features enabling registration of partitions within individual PCBs.
Production of even sharper edge patterns over a wide variety of resists requires DI systems with multi-wavelength light sources and high depth of focus capabilities. These advanced capabilities help the manufacturer maintain consistent uniformity, high quality, and high throughput.
AOI
Automated Optical Inspection systems enable PCB manufacturers identify HDI defects quickly and accurately for enhanced quality assurance, while reducing false alarms that could stall the production process. Additionally, employment of assessment capabilities such as 2D metrology enables continuous automatic inline measurements of conductor widths both at the top and bottom. This allows improved impedance control through repeatable and accurate measurements using streamlined sampling techniques.
AOS
Rush PCB also advises the employment of AOS or Automated Optical Shaping systems for effectively eliminating defects such as shorts, nicks, and opens. AOS systems with 3D shaping capabilities help to recreate the original design, which can also apply the inner and outer layers of HDI PCBs.
Rush PCB does not advise manual repair for HDI PCBs, as these are not accurate and may even damage the panel. On the other hand, AOS systems allow boosting the yield considerably with highly precise and high-quality shaping, virtually eliminating PCB scrap. All this creates a competitive cost structure benefiting the customer.
Summary
Evolving from 4G LTE to 5G demands a better approach to advanced HDI PCB manufacturing techniques that helps manufacturers maximize the density of the embedded electronics while reducing the loss of RF signals at high frequencies. Eminent PCB manufacturers such as Rush PCB are turning to mSAP for meeting these exacting requirements. Simultaneously, they are also deploying DI, AOI, and AOS technologies for lowering their manufacturing costs, accelerating their production throughput, and maximizing their yields.